ものづくり革新・改善の研修とコンサル, 研修
模擬ラインによるライン改善実践トレーニング研修
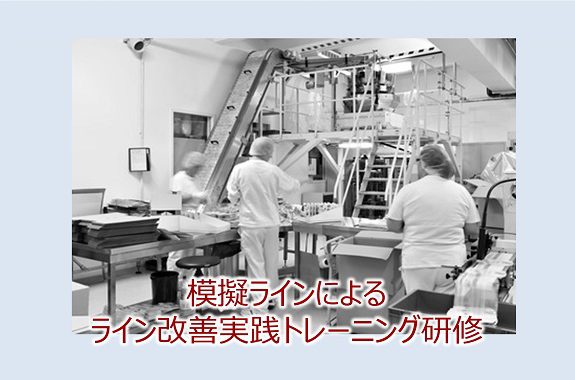
ものづくり力を飛躍的に高めるムダ取りと整流化改善力を身につける
実稼働ラインを対象とした改善は、止めることができないという理由から、小手先レベルの改善になりがちです。一方で、本格的なライン改善の経験者は少なく、ライン改善者を養成する場もありません。このような状況から、新設ラインの導入時や設備の更新時にのみ、時間をかけて本格的なライン改善をしているという企業は少なくありません。
トヨタ系では、ラインのレイアウト変更も含めた本格的ライン改善を一晩で行い、次の日、稼働させてみて、問題を洗い出し、その晩、また、ライン改善をするという改善のPDCAサイクルを毎日回しています。数ヶ月から数年に1回のライン改善と毎日のライン改善では、ものづくり力の成長スピードの違いは歴然です。
本研修では、トヨタの改善の基本ツールの標準3票を使った本格的なライン改善を模擬ラインで、実践的に習得し、日々の中で日々の中でムダ取り・整流化改善のできる改善リーダーを養成します。
本研修による変化・効果について~受講者の声~
【流通加工】
標準3票は、量産品を生産しているメーカーでしか使えないと思っていました。重要なことは、ラインを事実データで捉えて、事実から自分たちのめざす工程や作業を設計し、やってみて設計のまずさを直すことを繰り返すことです。そのことに気づいたとき、自分のラインですぐにやってみたくなりました。
【包装資材メーカー】
自分たちのものづくりのやり方が数十年来変わっていなくて、このままじゃダメだと焦っていました。でも、どうしても実績あるやり方を変えるのが怖くて変えられませんでした。研修では首尾一貫して、やってみた事実から改善策を考えました。経験や実績ではなく、今、目の前にある事実から考えることが自分たちに今一番必要なこととわかりました。
標準3票は、量産品を生産しているメーカーでしか使えないと思っていました。重要なことは、ラインを事実データで捉えて、事実から自分たちのめざす工程や作業を設計し、やってみて設計のまずさを直すことを繰り返すことです。そのことに気づいたとき、自分のラインですぐにやってみたくなりました。
【包装資材メーカー】
自分たちのものづくりのやり方が数十年来変わっていなくて、このままじゃダメだと焦っていました。でも、どうしても実績あるやり方を変えるのが怖くて変えられませんでした。研修では首尾一貫して、やってみた事実から改善策を考えました。経験や実績ではなく、今、目の前にある事実から考えることが自分たちに今一番必要なこととわかりました。
コースの概要
対 象 | ・改善推進責任者 ・現場の管理監督者・現場リーダー ・製造管理部門責任者・スタッフ |
研修形態 | 講師派遣型(オンサイト研修) |
研修時間 | 8時間 |
定 員 | 20名 |
研修の内容
1.標準作業と改善【講義】
・トヨタの改善スタイル=現地現物で自分たちの常識を打破する
・標準作業と作業標準の違い=標準作業は改善の出発点
・標準3票と標準作業改善のステップ
・一個流し(小ロット生産化)による変動対応力を高める意義と効果
2.表標準で現在のラインを明らかにして目標と課題の設定【講義と実習】
・模擬ラインの表標準を作ろう
>模擬ラインの作業の体験と時間観測
>工程別能力表、標準作業組合せ票、標準作業票の作成
>改善目標と課題の設定
3.ライン改善の実践【実習】
・模擬ラインで改善のPDCAを回そう
>模擬ラインの作業の要素作業分割・ECRSでの改善案の立案
>設備改善の仕掛け化改善案の立案
>標準3票の作成とシミュレーション
>模擬ラインでの改善案の実施
>模擬ラインでの改善効果の検証と更なる改善点の洗い出し
>改善の失敗ポイントをふり返り改善案の修正を繰り返す
4.改善結果の発表とふり返り【発表とグループワーク】
・自分たちの改善内容のまとめと発表
>改善前後の比較と効果
>改善の失敗からの学びと成功の秘訣
>自社のライン改善を成功させるためのポイントのまとめ
・トヨタの改善スタイル=現地現物で自分たちの常識を打破する
・標準作業と作業標準の違い=標準作業は改善の出発点
・標準3票と標準作業改善のステップ
・一個流し(小ロット生産化)による変動対応力を高める意義と効果
2.表標準で現在のラインを明らかにして目標と課題の設定【講義と実習】
・模擬ラインの表標準を作ろう
>模擬ラインの作業の体験と時間観測
>工程別能力表、標準作業組合せ票、標準作業票の作成
>改善目標と課題の設定
3.ライン改善の実践【実習】
・模擬ラインで改善のPDCAを回そう
>模擬ラインの作業の要素作業分割・ECRSでの改善案の立案
>設備改善の仕掛け化改善案の立案
>標準3票の作成とシミュレーション
>模擬ラインでの改善案の実施
>模擬ラインでの改善効果の検証と更なる改善点の洗い出し
>改善の失敗ポイントをふり返り改善案の修正を繰り返す
4.改善結果の発表とふり返り【発表とグループワーク】
・自分たちの改善内容のまとめと発表
>改善前後の比較と効果
>改善の失敗からの学びと成功の秘訣
>自社のライン改善を成功させるためのポイントのまとめ
研修のご相談/詳細カリキュラム・見積もりのお問い合わせ![]() ![]() |
Copyright © 改善と人材育成のコンサルソーシング株式会社