Blog
6.232019
コンカレントエンジニアリング成功のための2つの手法と進め方のコツ
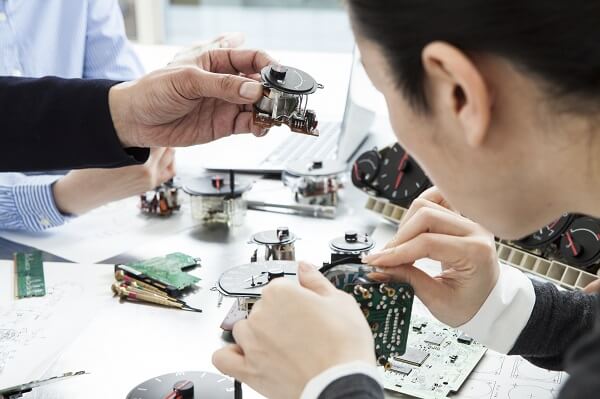
コンカレントエンジニアリング成功のための手法を図解で解説
コンカレント・エンジニアリングとは、企画、製品設計、工程設計、設備設計、生産準備など一連の開発から準備の活動を同時並行的に行い、相互に情報の共有と早期の課題形成と対策を行う活動を言います。
設計部門や生産技術や品質管理、工場部門間で情報を共有し、より早い段階で生産や運用、提供段階の問題を洗い出して改善するためのコンカレントエンジニアリング手法と進め方を図解を交えて紹介します。
<目次>
コンカレントエンジニアリングのための2つの手法
イレギュラーチェックリストの役割とコンカレントの進め方
イレギュラー分析のプロセスと視点
イレギュラー・チェックリストのつくり方
逆レジデント・エンジニアで生産・販売・運用のノウハウの共有
コンカレントエンジニアリングのための2つの手法
コンカレントエンジニアリングの目的は、より早い段階で生産や運用、提供段階の問題を洗い出して改善すること=源流管理にあります。
問題点を解決しただけでは、開発する製品・サービスの競争力は高まりません。競争力を高めるためには、多くの専門家のノウハウを盛り込むことが必要です。様々な専門家(各部門)より集めて開発や改善に盛り込むための手法(しくみ)が必要です。
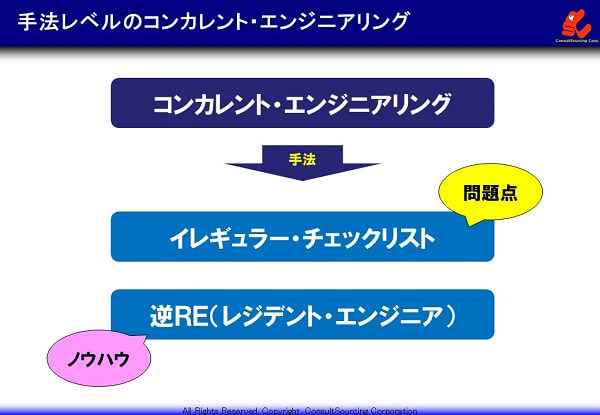
イレギュラーチェックリスト
イレギュラーチェックリストは、生産や運用、提供段階のイレギュラー事象である問題点を共有するための手法です。
生産段階や運用、適用段階において、製品やサービス、システムの品質や生産性、コストを劣化させたり、悪化させてしまう問題点を洗い出して、改善するための手法です。
逆レジデント・エンジニア
逆RE(レジデント・エンジニア)は、生産部門の技術者や販売部門、運用部門のスタッフなどが設計開発段階へ乗り込んで、生産や販売、運用などにおいて、製品やサービス、システムの品質レベルや生産性向上、コスト低減に貢献するノウハウを提案する方法です。
イレギュラーチェックリストの役割とコンカレントの進め方
設計開発で検出できです、下流のプロセスで発生する問題点について考えてみましょう。
企画や設計段階では、製品やサービスの基本機能や動作、条件での検討や設計が繰り返され、生産や運用、提供段階での変則事象への配慮が欠落することが多いです。
下流のプロセスでは、実行時における変則事象からの問題が多く発生します。
変則事象とは、正常な状態や規定された手順から外れたり、様々な条件などが重なって、適切な条件や方法で実行できない事象を言います。
例えば、ヒューマンエラーなどによって組付けを間違えてしまう。
加工液の劣化から初期の加工条件では適切な品質が確保できないなどです。
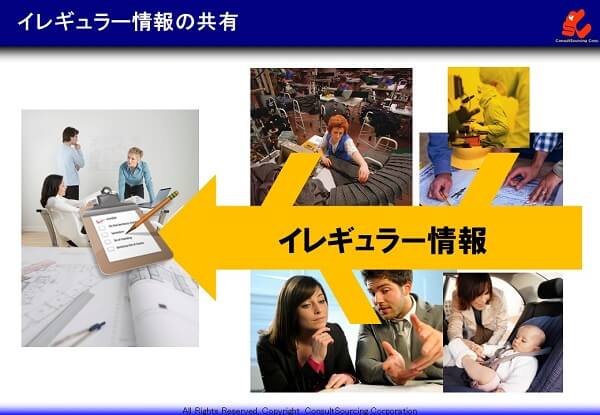
変則事象に関する情報をリストアップして設計開発部門へ提供し共有することが必要です。
実行時の変則事象に関する情報を伝えることで、下流のプロセスでの問題発生を減らす事ができます。
下流のプロセスの変則事象をリストアップし、設計開発段階へ伝えるものがイレギュラー・チェックリストです。
イレギュラーチェックリストによって、下流のプロセスの問題点を洗い出し、上流プロセスに前倒しすることができます。
源流管理のめざす、源流で問題点を見つけてつぶして、品質をつくりこむ開発ができるようになります。
イレギュラー分析のプロセスと視点
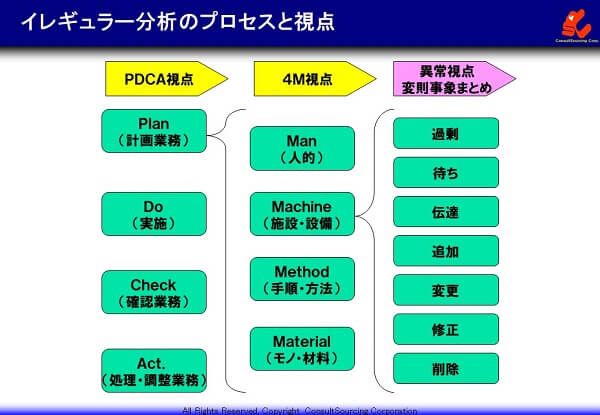
イレギュラー・チェックリストをつくるためには、実行時の変則事象であるイレギュラーを洗い出さなければなりません。
これは、設計開発部門の担当者だけではできません。
営業、生産技術、品質管理、製造、物流など様々な関連部門の協力が不可欠です。
関連部門の協力のもと、イレギュラーの分析をしなければなりません。
関連部門の専門的な視点や経験に基づいてイレギュラーチェックリストがつくられます。
イレギュラーチェックリストを通じたコンカレントエンジニアリングを行う事ができます。
イレギュラー分析は、業務をPDCA視点で分解し、イレギュラーの起点を4M視点で分析して、異常現象をもとにイレギュラー事象をまとめます。
まず、業務をPDCAに分けます。すべての業務にはPDCAのプロセスがあります。
計画業務と実行、確認や処置、調整は、それぞれプロセスの目的や性質が異なります。
PDCAに分けて考えることで、起きる事象をイメージしやすくなります。
次にPDCAのプロセス毎に、イレギュラーの起きる原因やキッカケとなることを4Mの視点で分析します。
そして、イレギュラーの原因が重なったり、かみ合ったりしたときに表れるイレギュラーの事象を整理してまとめます。
イレギュラー・チェックリストのつくり方
イレギュラー・チェックリストの構成
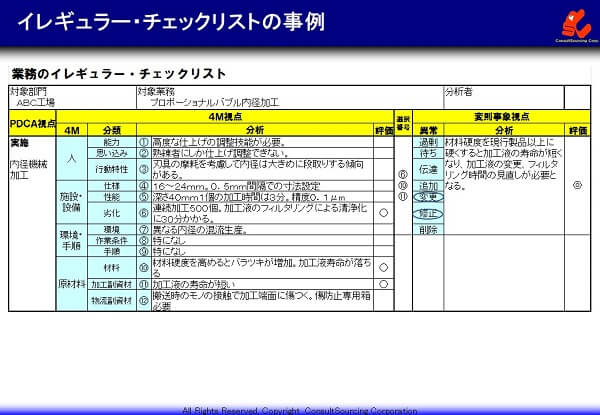
これは、イレギュラー・チェックリストの事例です。
対象となる業務毎に作成します。
開発する製品やサービスの生産や運用、提供段階における業務を対象としてイレギュラーを洗い出します。
まだ、該当する業務が無い場合は、よく似た製品・サービスの業務から類推して作成します。
似た製品やサービスが無い場合は、試作品やイメージ図などを参考にして、経験者が類推して作成します。
左から右に向かって整理・分析しながら作成していきます。
まず、業務をPDCAに分解して、次に、4Mの視点でイレギュラーの原因を分析し、最後に変則事象としてまとめます。
業務をPDCAで分解して考える
それでは、イレギュラーチェックリストを作成する手順を説明をします。
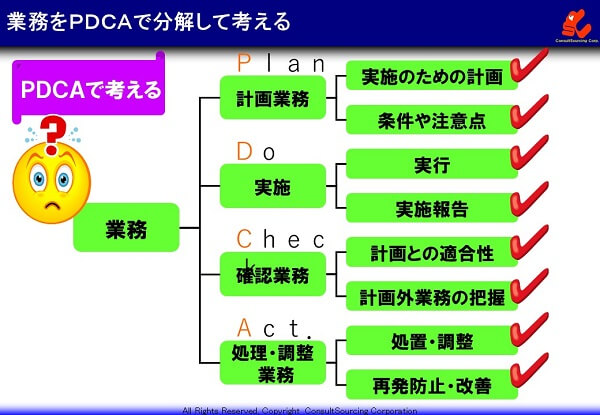
最初は、業務をPDCAで分解します。
どのような業務も必ずPDCAで考えると容易にプロセスに分解することができます。
PDCAの分解は、対象となる業務毎にPから順番に分解整理していきます。
Pは計画業務です。実行するための計画で、手順や方法、日程、担当などをどのようにするかあらかじめ決める事です。
計画では、特に配慮すべき条件や注意点を明確にして、その条件や注意点に基づいて、手順や方法、日程などを決めていきます。
この条件や注意点を決める事も計画です。
計画は、必ず、計画書などの文書があるわけではありません。無い場合が多いです。自分で考えて決めたことも計画です。
Dは実施です。計画した事を実行する事です。実行したことを記録し、報告する事です。
Cは確認業務です。計画との適合性を確認します。計画に対する抜けやズレ、間違いがないかを確認する事です。
計画外の業務がされていないかも確認します。
Aは処理・調整業務です。
確認業務によって明らかになった、問題などに対して、それを正すため、影響を無くすための処理や調整をすることです。
次回に向けての再発防止などの改善をすることも含まれます。
変則事象の起点を4Mで考える
次に、PDCAに分解されて業務毎に、イレギュラーの発生する原因やキッカケを、4Mの視点で分析します。
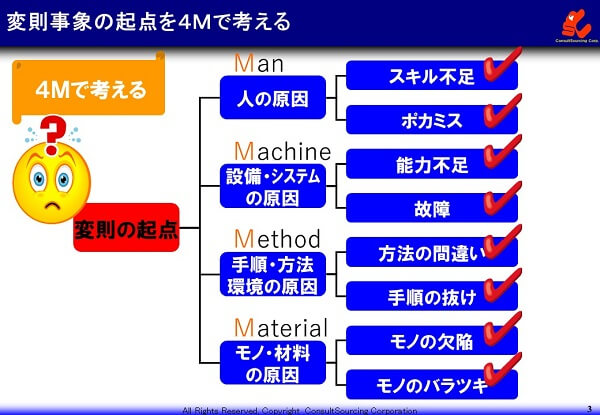
4Mとは、人、設備・システム、手順・方法・環境、モノ・材料の4つの視点の事です。
分析する順番は、特にありません。考えやすい順番で分析してください。
ここでは、人から順番に下へと説明していきます。
人の原因では、人を起点として、イレギュラーが発生する事を考えます。
人の能力、スキルなどが原因となって、正常な状態や規定された手順から外れたり、適切な条件や方法で作業できない事が起きる可能性があるかを考えます。
思い込みやポカミスなどのヒューマンエラーや人の行動特性からの原因も考えます。
設備・システムの原因は、設備のもともとの性能や能力に起因すること、性能や能力の経年劣化や故障などが原因となって引き起こされる事を分析します。実際の設備でよく起きているトラブルや寿命などの情報を集めて整理する事も大切です。
手順・方法・環境の原因では、手順や方法が原因となって引き起こされる事を検討します。
手順・方法は、技術や設備の進歩によって変わっていきます。また、品質や生産性の改善によって変更される事もあります。
手順・方法は、その変更などによって被るダメージの大きさなども考慮し、変更する場合の処置やバックアップの有無が引き金となることも検討するようにします。
モノ・材料の原因は、モノや材料の欠陥や品質や性能のバラツキなどの原因について検討します。
明らかに欠陥などは、問題となる事は少ないですが、規格内の偏りやバラツキなどが原因となる場合、規格で規定されていない成分や特性による影響の有無なども検討します。
変則事象を整理する
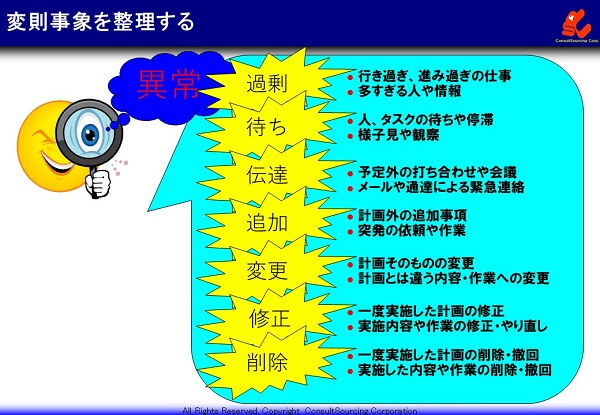
原因だけが伝えられても、それによってどのようなイレギュラーが発生するかイメージできなければ、対策案を検討する事はできません。
最後に、業務毎の4M分析をもとに、イレギュラーとしてどのような変則事象となって表れるか整理してまとめます。
正常な状態や規定された手順から外れたり、適切な条件や方法で作業できないということがどのような形で表れるかをまとめます。
変則事象をまとめるときは、異常現象をイメージするとまとめやすくなります。
4M分析した原因が絡み合って、どのような現象として表れてくるかを考えましょう。
何か過剰な事は起きませんか?行き過ぎ、多すぎることはありませんか?
手待ちなどはありませんか?タスクが処理されず止まったり、人が手待ちになったりしませんか?
伝達が増えませんか?予定外や打ち合わせ、会議の増加、緊急連絡が増えませんか?
何か追加されることが起きませんか。計画外の処置やプロセス、作業、部品の追加はありませんか?
変更は発生しませんか?製品・サービスの仕様や内容、生産プロセスやサービス手順の変更などはありませんか?
修正しなければならなくなる事はありませんか?一度つくったモノや提供したモノを修正したり、やり直したりすることはありませんか?
作成したモノや提供したモノを削除したり、回収したりすることはありませんか?
このような異常現象を参考に、起きる可能性のあるイレギュラーを整理してまとめて、イレギュラー・チェックリストを完成させます。
イレギュラー・チェックリストは、設計・開発部門を含めて全体で共有し、開発製品やサービスの問題点の洗い出しに使います。
発見された問題点は、可能な限り源流側で対策できるように改善を行います。
逆レジデント・エンジニアで生産・販売・運用のノウハウの共有
イレギュラー・チェックリストの主なねらいは、下流のプロセスで発生する問題点を減らす事です。
生産や運用、提供段階において、正常な状態や規定された手順から外れたり、様々な条件などが重なって、適切な条件や方法で実行できない事象を洗い出して、設計・開発段階でつぶす事が目的です。
これは、主にマイナス面の改善です。
開発する製品やサービス、システムのマイナス面を改善する事で、トラブルは減り、立ち上がりもスムーズになります。
しかし、マイナス面だけの改善では、競争力は高まりません。
生産や運用、適用段階において、今以上に、品質レベルや生産性を高め、コスト低減を図るノウハウやポイントがたくさんあります。
そのノウハウやポイントを、設計・開発段階に盛り込むことも必要です。
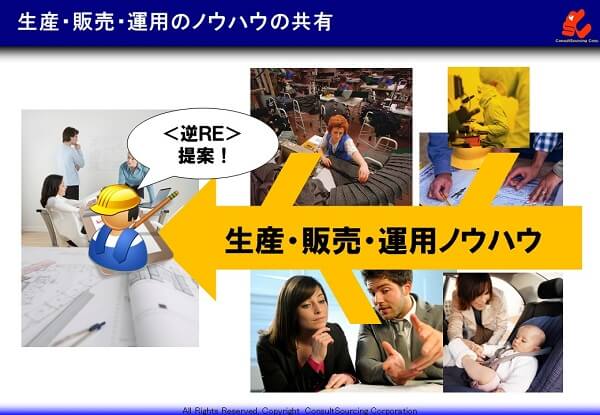
イレギュラー・チェックリストでは、このノウハウを洗い出して提案する事はできません。
このノウハウを提案するのが逆REです。
REとは、レジデント・エンジニアの略で、専従駐在技術者という意味です。
具体的には設計者が、工場へ派遣され、生産準備段階、生産段階の問題に対して、その場ですぐに対応できる体制をとることです。
逆REとは、逆に工場部門の技術者、販売や運用部門のスタッフなどが設計開発段階へ乗り込むことです。
生産準備での工程設計や作業設計、品質管理計画を行う技術者が設計部門に常駐し、生産や運用、提供段階でのノウハウを抽出し、抜本的対策を設計へ盛り込むことです。
*関連動画(さらに詳しく↓↓)
イレギュラーチェックリストについてもっと知りたい方は、動画ラーニングチャンネルで公開中の「コンカレントエンジニアリングの実践ツールの使い方」の無料講座をご覧下さい。
Copyright © 改善と人材育成のコンサルソーシング株式会社