Blog
12.52019
人時生産性とは~計算式と分析方法のツールと事例
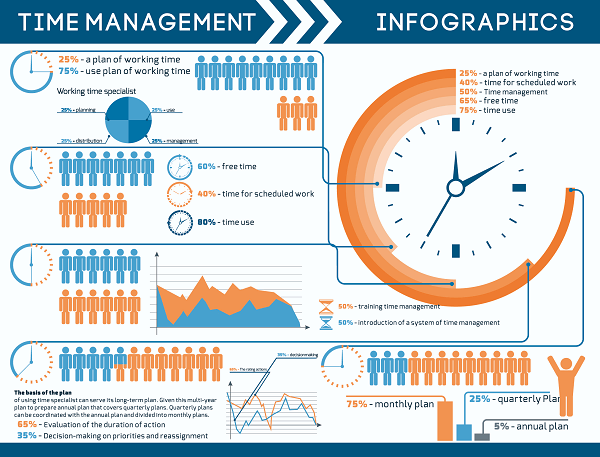
管理や生産性改善に役立つ人時生産性の計算・分析方法
人時生産性は、仕事の効率性を測るモノサシです。管理や改善を行うためには、現在の状態や改善前後の変化を客観的に測定評価することが必要です。
人時生産性は、仕事を客観的に測定評価するモノサシとして、最も有効な指標です。
ここでは、管理や生産性改善に役立つ人時生産性の計算方法・分析方法を紹介します。
<目次>
人時生産性とは
人時生産性のための人の動きとロスの見える化
ワークサンプリングにて動作のムダを見える化する
時間観測にて動作のムダを見える化する
ビデオ撮影による動作分析
人と機械の動きの組合せの分析
製造における人時生産性の実際
人時生産性とは
人時生産性とは、従業員一人が1時間働いたときに、どれだけの付加価値(粗利益=営業総利益)を稼いだかを計る指標です。
仕事の効率性を計るモノサシと言えます。
ここでの付加価値とは、粗利益、会計的には営業総利益というもので、売り上げ金額から仕入れ金額を引いた値となります。原材料に対して、社内で、設備や人手を使って、価値を高めた金額を表します。
人時生産性を測定する目時は、データを分析し、課題を洗いだし、改善を行うことにあります。
ですから、会社全体の人時生産性を測定するよりも、部門や職場、ライン、チーム、人毎の人時生産性を測定し、ムダを洗い出して、具体的な改善課題を明確にすることに意味があります。
人時生産性の計算式と分析の仕方
人時生産性の計算式は
評価期間の営業総利益÷評価期間の総労働時間
となります。
評価期間を1ヶ月単位でみる場合は、ムダの洗い出しとともに人時生産性が適切に維持され、改善によって高まっているか管理することも目的です。
1週間や1日単位でみる場合は、突発的異常などによって、人時生産性が急激に低下していないか、監視することが目的となります。
代表的な人時生産性の分析の仕方には以下の3つがあります。
観測値と平均値の差異分析
業務内容を観測し、各作業や動作の時間を計測して集計した労働時間を使って算出した観測値ベースの人時生産性と評価期間の総労働時間を使って算出した平均値ベースの人時生産性を差異を分析する方法です。
経験的に、観測値ベースの人時生産性の1.2~1.5倍が平均値ベースの人時生産性となります。
これよりも差異が大きい場合、業務管理上に大きな欠陥があり、業務の手順や方法を改善しても効果がなく、管理方法の問題を解決することを優先しなければなりません。
時間的推移の分析
人時生産性の時間的推移を分析する方法です。
連続して低下傾向にある場合は、業務を繰り返す毎に手間が増えるなど、何か問題が積みあがっていること示しています。
周期性のある高低のある場合は、その周期に関連した問題や傾向が根底にあることを示しています。例えば締め日に業務が集中するなど。
不規則な高低=バラツキがある場合は、業務の標準化や教育が不十分なために不安定状態にあることを示しています。
層別比較分析
製品・サービス、ラインや職場、チームや個人などの人時生産性を比較し、その違いから、それぞれが抱えている問題や傾向を洗い出すために行います。
それでは、人時生産性を高めるために役立つ「見える化のしかけ」を紹介します。
人時生産性のための人の動きとロスの見える化
人時生産性を高めるためには、人の動きを観察し、ムダとなるロスの見える化します。
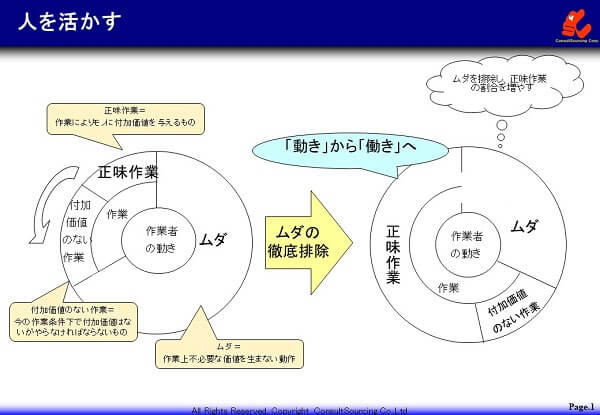
人の動きを分類
人の動きには、
・正味作業:作業によりモノに付加価値を与えるもの
・付加価値のない作業:今の作業条件下で付加価値はないがやらなければならないもの
・ムダ:作業上不必要な価値を生まない動作
というように分けることができます。
人時生産性を低下させる5大ロス
ムダは人に関するロスとして、
管理ロス
生産管理や発注管理など管理上の理由から発生する手待ちのロス
動作ロス
従業員の作業動作のムダによって発生するロス
編成ロス
仕事の分担や生産量の変動などによって、仕事の負荷のバランスが崩れることにより発生するロス
自動化置き換えロス
人手による作業のうち、機械化や自動化に置き換えることによって、品質や生産性が高まるにも関わらず、機械化や自動化をしないことによって発生するロス
測定・調整ロス
生産において測定と調整を繰り返し行うことによって発生するロスなどに分けることができます。
日常の仕事が当たり前になってしまうとこのようなムダに気づくことなく見過ごされがちです。
そこで、人の動きを見える化し、ムダを排除することで正味作業の割合を高め、従業員が忙しそうには動いているが価値を生んでいない状態から、付加価値のある働きの割合を高めていきます。
動作分析の進め方
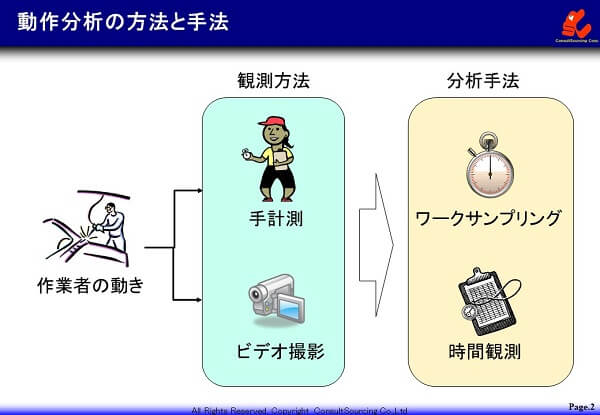
人の動きのムダを見える化するツールが、動作分析です。
手計測では、従業員の後ろに立ち黙ってジッと観察します。
しかしながら、いきなりこれをすれば、従業員は自分が「何か悪いことでもしたのなあ?」と不安になります。
そこで、始める前には「あなたの動きを分析して楽になるような改善をするために動作を見させて下さい」というように時間観測の趣旨を説明してから行います。
動作分析の進め方は、以下の通りです。
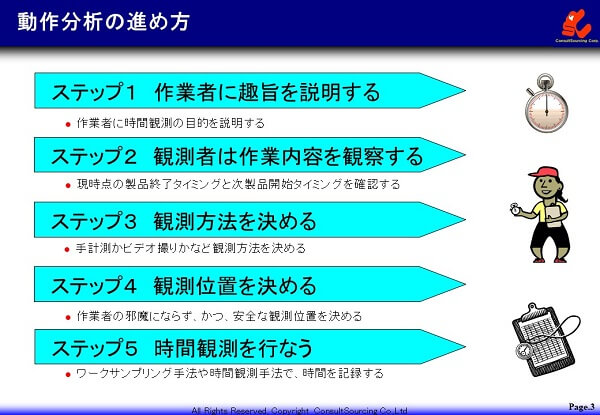
ワークサンプリングにて動作のムダを見える化する
ストップウォッチを用いて時間観察しながら動作分析する手法の一つです。
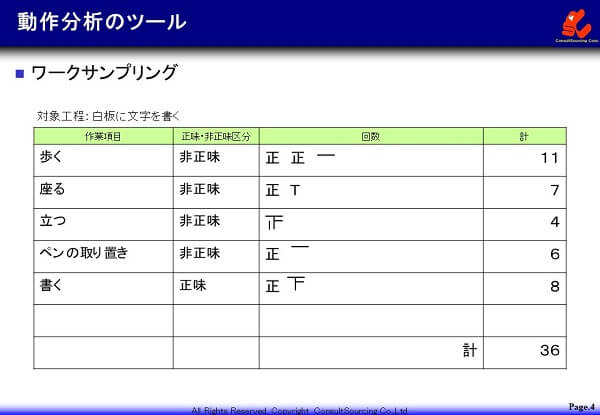
ワークサンプリング手法
ワークサンプリングは、人の動きを瞬間的に観測し、それらの観測の積み重ねによって、各観測項目の時間構成や作業構成比率、その推移状況などを統計的に推測する方法です。
進め方の手順は、以下の通りです。
①観測する対象と範囲を決定する
どの職場、工程、時間帯、人を対象にするか。
②観測する作業項目を決定する
作業項目は把握したい作業の大きさにし、何が正味作業か非正味作業なのか区分する。
③観測間隔・時間を決める
例えば、30秒間隔で10分間というように決める。
④観測する
客観的に瞬間的に観測し回数を記録していく。
必要ならば説明を求めても良い。
打合せや不在の場合は理由を聞く。
観測項目は臨機応変に追記していく。
対象従業員には帽子の色を変えるなど分かりやすくする。
⑤観測値の集計・分析を行う
観測項目ごとの全体に対する正味/非正味、作業別、動作別、機械別など比率を出してグラフ化する。
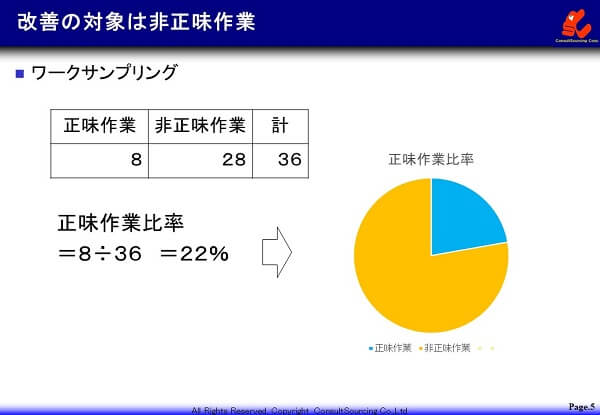
改善の対象は非正味作業
ワークサンプリングでは、非正味作業が見える化されます。
本例では、「書く」という正味比率は約2割程度しかなく、残りの8割は、「歩く・座る・立つ・ペンの取り置き」などの非正味作業です。
これらを更に細かく見ていくと些細な動作にムダが潜んでいます。
例えば、
・足の動き:空歩行、半歩戻り、半歩踏み込み、立ち止まり
・手の動き:上下、片手の手待ち、保持、持ち替え、繰り返し、取りにくい、やりにくい、放れ際
・体の動き:振り向き、かがみ、背伸び、大きな動き、重いものの運搬、引っ張り、不安全動作
・目の動き:探す、選ぶ、確認、見にくい、狙い、気をつかう、いらいら
・モノの動き:上下、左右、反転、方向転換、取り置き
などです。
このようなムダをブレーンストーミングなどで抽出し排除し、正味作業比率を高めていくことで、付加価値の割合が増していきます。
時間観測にて動作のムダを見える化する
ストップウォッチを用いて動作分析するもう一つの手法です。
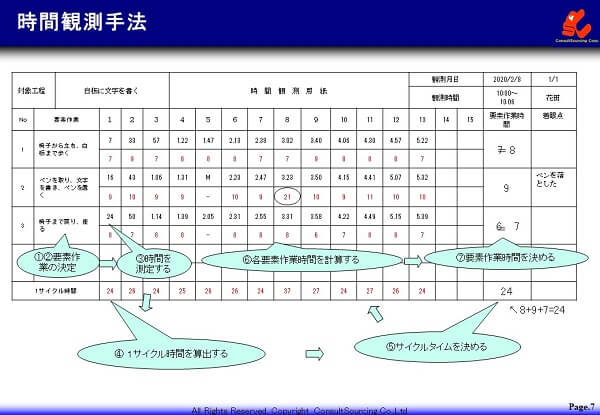
時間観測手法
ワークサンプリングが構成比率による推測方法であったのに対し、時間観測手法は、仕事の順序を記録し時間を直接測定し把握します。
進め方の手順は、以下の通りです。
①要素作業を決定する
要素作業は観測可能な大きさ(少なくとも2~3秒以上)にする。
②観測用紙へ要素作業を記入する
観測点(ストップウォッチを読み取る瞬間でその作業が終った瞬間)を記憶する。
③時間を観測する
ストップウォッチは途中で止めずに回し続け要素作業が終わった時のストップウォッチの目盛りを読み、観測用紙の観測時間記入欄(上段)へ黒字で記入する。
④1サイクル当たりの時間を求める
最下段に赤字で1サイクル時間を記入する。
⑤サイクルタイムを決める
10回程度観測しその最小値を選び、要素作業時間欄の最下段へ記入する。
⑥各要素作業の時間を求める
下段の時間値から上段の時間値を引算し各下段へ記入する。
⑦各要素作業時間を決める
各要素作業時間はサイクルタイムに合わせること。各要素作業の最小値を足しても必ずしもサイクルタイムと同じ値にならない場合は要素作業時間の発生頻度の多い順に割り振る。
改善の着眼点はバラツキ
時間観測手法では、同じ人でも毎回時間が異なる、またできる人と不慣れな人では時間が大きく違ってくるというようなバラツキが見える化されます。
そこで、現状把握として、
・What:何が (どの要素作業が)
・When:いつから、いつ (いつが良くて、いつが悪いのか)
・Where:どこで (どこが良くて、どこが悪いのか)
・Who:誰が (誰がやると良くて、誰がやると悪いのか)
・How:どのように (どうやると良くて、どうやると悪いのか)
・How Much:どのくらい (何秒、何分差があるのか)
という観点で分析し、バラツキの大きな点に対する動作のムダ排除の改善を施します。
改善後は、再度時間観測を行い、Before/Afterで効果の確認を行います。
ビデオ撮影による動作分析
ビデオ撮影した後で再生しながら従業員を観察する手法です。
ビデオ撮影の仕方
観察者と従業員が1対1の関係になって一人の動きを追うやり方や、三脚を邪魔にならない場所に設置して人が張り付かずに録画するやり方などがあります。
特に、ビデオ観測が向いているのは、以下の場合です。
・繰り返し性が高く、1サイクル時間が短い作業観測の時
・動作まで細かく分析する時
・長時間で頻度の少ない作業の時
・改善前後の比較をする時
・多人数で議論する時 など
ビデオ再生からの分析
ビデオの利点は、早送りや巻き戻しができることです。
例えば、1日かけて段取り替えを行う作業では、早送りで再生すれば短時間で1日分の動きを圧縮して見ることができます。
微妙な動きでは、何度も巻き戻して再生できます。
再生時に本人にも自身の動きを見せることができ、自分の動きのムダを自覚させることもできます。
このように観測方法には、手計測とビデオ撮影、分析手法には、ワークサンプリングと時間観測があります。
業種業態、作業内容に応じてどの観測方法がよいか、どの分析手法がよいか状況に応じて選択し、非正味作業やバラツキを見える化し、改善を実施します。
人と機械の動きの組合せの分析
人の動きと機械の動きの中でムダを見える化します。
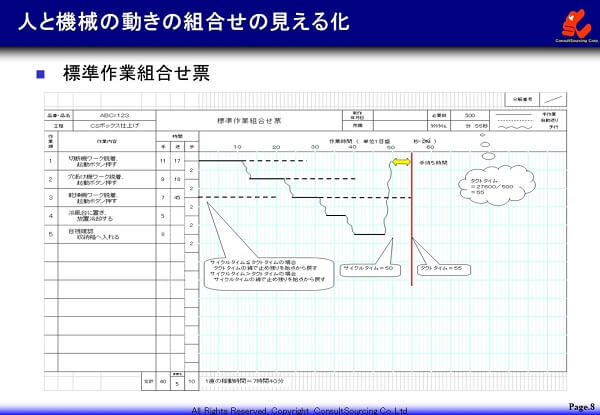
標準作業組合せ票による分析
人と機械の動きの両面からムダを見つけるツールが、標準作業組合せ票(マン・マシンチャート)です。
標準作業組合せ票とは、各工程の手作業時間や歩行時間を明らかにし、タクトタイム(1個どれだけの時間でつくればよいかという標準スピード)を基にして人と機械の動きを組合せ、従業員一人がどれだけの範囲を担当し、作業順序をどのようにするかを検討する道具です。
タクトタイムとサイクルタイム(実際に行った実績時間)の差が改善ニーズとなり、サイクルタイムをタクトタイムに近づける作業改善(歩行のムダをとる、手待ちをなくすなど)の必要箇所が見える化されます。
また、自動送り時間との関係から、タクトタイム内にその作業の組合せが収まるかどうかも見えるようになります。
標準作業組合せ票の作成方法
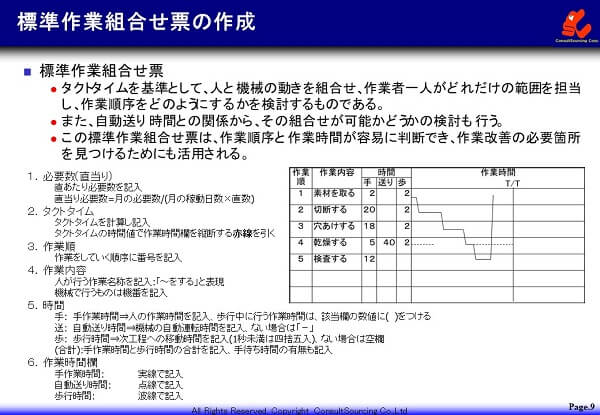
標準作業組合せ票は、以下の手順で作成します。
①直当り必要数を記入する。
②タクトタイムを求め記入する。
③作業順を記入する。
④作業内容を記入する。
⑤時間を記入する。
・手:手作業時間(人の作業時間)
・送:自動送り時間(機械の自動運転時間)
・歩:歩行時間(次工程への移動時間)
・合計:手作業時間と歩行時間の合計
⑥作業時間欄を記入する。
・手作業時間:実線
・自動送り時間:点線
・歩行時間:波線
製造における人時生産性の実際
人時生産性を測るモノサシで今の状態とロスの見える化して、生産性改善を行います。
製造における人時生産性で使う指標
製造における人時生産性のモノサシは、生産高(生産金額)で行うことが多いです。
本来は、粗利益(≒付加価値生産高)で行うべきものですが、以下の理由から生産高で行うことが多くあります。
①製品の粗利率は通常、一定であるため、生産性の変化を見る上では、生産高でも見ることができる。
②製品によって粗利率が異なる場合、生産する製品が異なると生産性が変動してしまい、製造現場の生産性の管理状態がみえなくなってしまう。
そこで、人時生産性=生産高(生産金額)÷投入工数(人x時間)で算出します。
ただし、経営としては、利益率の低い製品を生産していること自体のロスも含めて評価しなければならないので、粗利益で計算した本来の人時生産性も算出して評価しなければならない。
人時生産性を算出して見せる化する方法
①目的を明確にする:職場、月日、品種など、何を見たいかはっきりさせる
②アウトプットを明確にする:生産高、生産数など産出要件を決める
③インプットを明確にする:作業工数、従業員数など投入要件を明らかにする
④算出する:アウトプット÷インプットで人時生産性を計算する
⑤結果を分析する:算出結果の良し悪しを分析する
というようにして日々グラフ化し、時系列比較や職場間比較で異常を発見します。
例えば、ある工程で、生産高日あたり2,600個、定時7.5時間、従業員数3人の場合、
2,600÷(7.5×3)=115個/人・時間となり、一人で1時間あたり115個生産していることになります。
これを基準にして、生産高が減れば少ない工数(人数)で115個/人・時間を目指し、生産高が増えれば残業や増員で115個/人・時間をすることを目指します。
例えば、生産高が2,000個に減り同じ工数7.5時間で3人であれば、人時生産性は88個/人・時間となり、生産性が悪化した(さぼっている)ことが一目で分かります。
この場合は、2,000個を2人作業で残業を2.5時間プラスして行えば、人時生産性が同じような数字{2,000個÷(7.5時間×2人+残業2.5時間≒114個/人・時間)}なりますので、計画から一人抜いてその人には朝から別の作業をさせるようにします。
人の5大ロスを見える化するための指標例
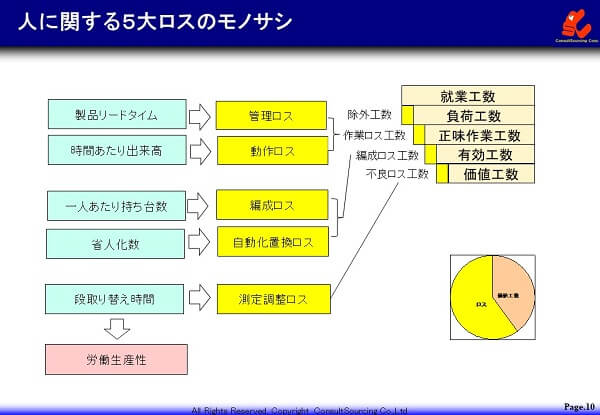
人時生産性の低いところがあったときは、以下の指標で分析することで、生産性を低下させている原因をつかむことができます。
①管理ロス:製品リードタイム(材料~完成品になるまでの時間)
②動作ロス:時間あたり出来高(1時間でいくつできたかという生産量)
③編成ロス:一人あたり持ち台数(一人で何台の機械を持つことができたか)
④自動化置き換えロス:省人化数(人を何人省くことができたか)
⑤測定・調整ロス:段取り替え時間(段取り替えに要した時間)
Copyright © 改善と人材育成のコンサルソーシング株式会社