Blog
12.32018
受注生産のための「かんばん方式」の導入方法と事例
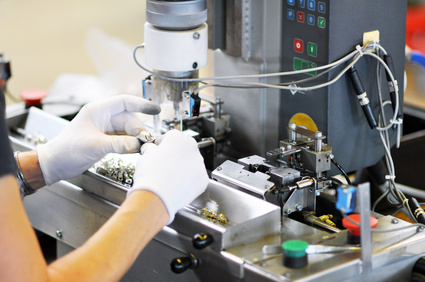
受注型・多品種少量生産にトヨタの「かんばん方式」を適用する方法
受注型・多品種少量生産に同一アイテムの「繰り返し生産」を前提とした「かんばん方式」は使えません。
しかし、「かんばん」の役割を一部変え、製造指示書と組み合わせることで、受注型・多品種少量生産にもトヨタ生産方式の「かんばん方式」が適用でき、その効果を得ることができます。受注型・多品種少量生産の「かんばん」の役割と運用方法を事例を交えて紹介します。
<目次>
受注型・多品種少量生産の「かんばん方式」とは
かんばんの構成
受注型・多品種少量生産の「かんばん」の要素
製造指示書と「かんばん」の関係
かんばん方式における流れと置き場
受注型・多品種少量生産のかんばん方式の運用方法
受注型・多品種少量生産の「かんばん方式」とは
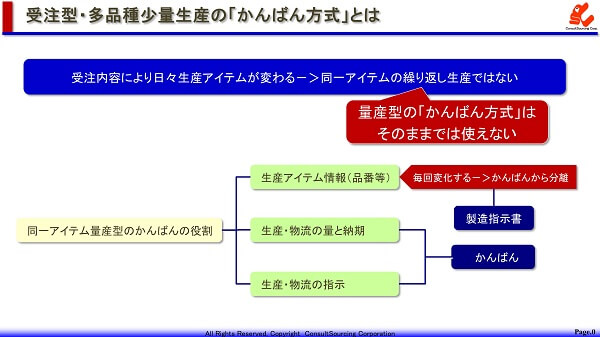
受注型・多品種少量生産の特徴は、受注内容により日々生産アイテムが変わることにあります。
自動車業界の量産のような同一アイテムの「繰り返し生産」を前提とした「かんばん方式」は、そのままでは使えません。
量産型の「かんばん方式」との違いは「かんばん」の役割の違いにあります。
「かんばん」の役割には、品番など生産アイテム情報の伝達、生産及び物流の量と納期の伝達、生産及び物流の開始、または、停止の指示の3つがあります。
この中で、生産アイテムについては、生産するモノが受注状況により、毎回変わってしまうことから「かんばん」に含めることができません。
そのため、「かんばん」には、残りの生産及び物流の量と納期の伝達、生産及び物流の指示の2つだけの役割をもたせることになります。
生産アイテム情報の伝達は、「製造指示書」として注文ごとに作成・発行し、「かんばん」と組み合せて生産現場へ出していきます。
ただし、「電子かんばん」など、都度発行の「かんばん方式」の場合は「製造指示書」と「かんばん」を一体化させた形で運用できます。
かんばんの構成
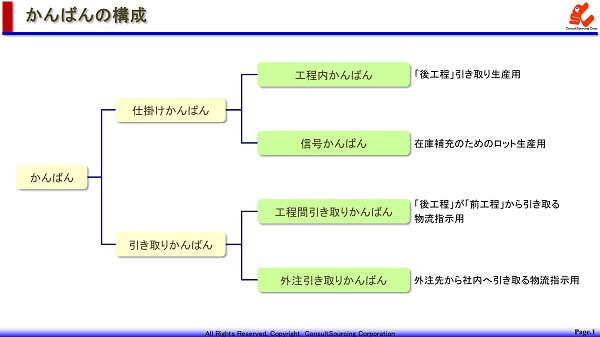
トヨタ生産方式の「かんばん方式」では、主に「仕掛けかんばん」と「引き取りかんばん」が使われます。
「仕掛けかんばん」には、「工程内かんばん」と「信号かんばん」があります。
「工程内かんばん」は、「後工程」引き取り生産のための「かんばん」で「引き取りかんばん」などによって、「後工程」から注文のあった製品の生産を指示するものです。
「信号かんばん」は、在庫量を維持するために規定在庫量を下回ったときに生産の指示をするためのものです。
「引き取りかんばん」には、工程間「引き取りかんばん」と外注「引き取りかんばん」があります。
工程間「引き取りかんばん」は、「後工程」が「前工程」から製品や部品を引き取るための物流指示用の「かんばん」で「後工程」から「前工程」への注文書のようなものです。
外注「引き取りかんばん」は、同じく、自社が外注先から部品や材料を引き取るための物流指示用の「かんばん」です。注文書のような機能がありますが、商取引上の問題があるので、あくまでも物流指示として扱い、注文書は別の形で発行します。
受注型・多品種少量生産の「かんばん」の要素
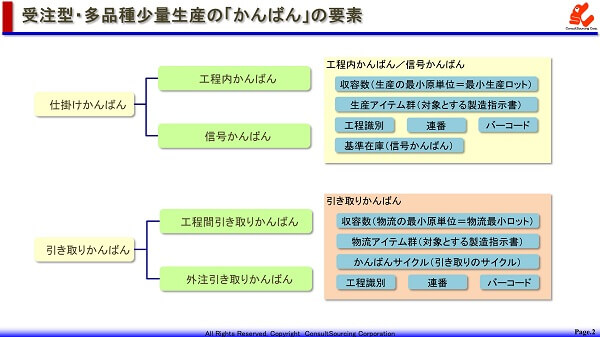
それでは、受注型・多品種少量生産の「かんばん」に盛り込む要素を見ていきましょう。
「仕掛けかんばん」に含めるものの最初は、収容数です。
これは、1枚の「かんばん」によって指示する生産量で、生産完了品が納められた容器や台車に収容する数量のことです。「かんばん」はこれら容器や台車に1枚、貼り付けられます。
収容数は、生産するときの最小の原単位となります。最小の生産ロットとも言えます。
生産アイテム群は、「かんばん」の運用対象となる製造指示書を特定することのできる情報を指します。
運用対象の工程を識別できる情報。
発行されている「かんばん」を特定し識別するのが連番です。
連番は、かんばんの総量を管理するために追加したり、間引いたりするときに使います。
生産システムと連動させるのがバーコードです。
ICチップなどを使う場合もあります。
「信号かんばん」では、基準在庫も含まれます。
「引き取りかんばん」に含めるものは収容数です。
「引き取りかんばん」の収容数は、1枚の「かんばん」で運搬する数量のことです。
「かんばん」は、物流のための容器や台車に貼り付けます。
物流の最小の原単位となります。最小の物流ロットとも言えます。
物流アイテム群は、「かんばん」による運搬対象となる製品指示書を特定することのできる情報を指します。
「かんばん」サイクルは、「かんばん」によって、製品や部品を引き取るサイクルを示したものです。
工程間の納期としての役割があります。
工程識別は、運用対象の工程を識別できる情報です。
発行されている「かんばん」を特定し識別するのが連番です。
連番は、かんばんの総量を管理するために、追加したり、間引いたりするときに使います。
生産システムや物流システムと連動させるのがバーコードです。
ICチップなどを使う場合もあります。
製造指示書と「かんばん」の関係
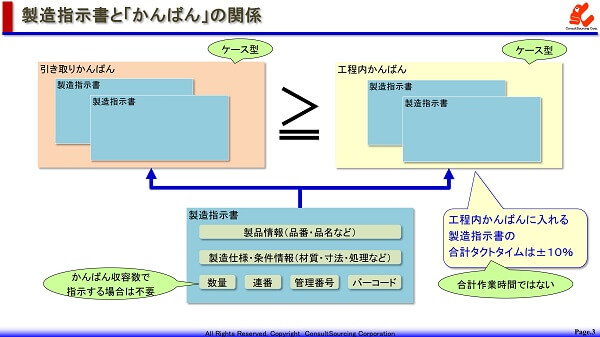
製造指示書に記載される情報を見ていきましょう。
製品情報は、品番・品名など生産する製品や部品を特定するための情報です。
図面や手順書などと整合させて、つくり方や管理方法がわかります。
製品情報だけでは明確にならない材質、寸法、処理などの製造仕様・条件情報は、注文において個別に指定される仕様・情報などです。
数量は、1回の投入で生産する量です。
「工程内かんばん」の収容数で指示する場合は不要となります。
発行されている「製造指示書」を特定し識別するのが連番です。
連番は、納期順にふられ、若い番号ほど納期が早いものとなります。
生産の投入順や物流での運搬順をスケジューリングするときに使います。
管理番号は、注文情報と製造指示書を紐付けるための番号です。
生産システムや物流システムと連動させるのがバーコードです。
「かんばん」と製造指示書を紐付ける場合にも使います。
製造指示書は「かんばん」に入れて使います。
ですから、「かんばん」はケース型となることが多いです。
同じ工程で運用される「工程内かんばん」は、すべてタクトタイムが揃っている必要があります。
ですから、「工程内かんばん」に入れる製造指示書の合計タクトタイムは、±10%以下になるようにします。
タクトタイムを揃えることで生産負荷のバラツキを無くして、平準化できます。
「かんばん」の枚数から作業量や納期がわかり、計画や管理がしやすくなるのです。
タクトタイムとは、工程からモノができあがってくる間隔の時間で、作業時間や加工時間のことではありません。異なる作業時間や加工時間であっても、手持ちや組み合わせなどによってタクトタイムを揃えることはできます。
「引き取りかんばん」は、1枚ないし、2枚以上の「工程内かんばん」の運搬を行います。
ですから、「引き取りかんばん」に入れられる製造指示書は「工程内かんばん」の入っている製造指示書と同じか、それ以上の枚数を入れることになります。
かんばん方式における流れと置き場
続いて、かんばん方式における、「かんばん」とモノの流れ、置き場を見ていきましょう。
事例は、椅子メーカーの組立工程と塗装工程からなるラインです。
モノとかんばんの置き場
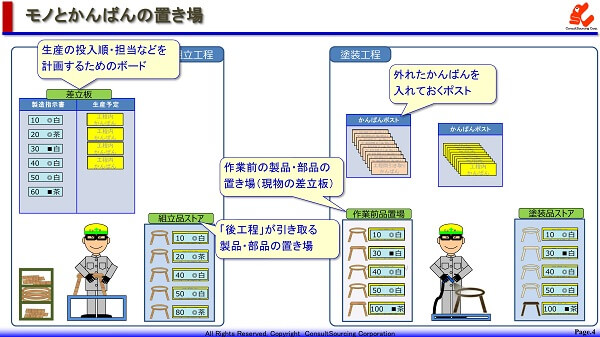
かんばんポストは、ストアなどから外れた「かんばん」を入れるところです。
「かんばん」の出発点となります。「かんばん」を追加したり、間引いたりするのも、ここで行います。
差立板は、「かんばん」と製造指示書を組み合わせて、投入順や担当などを計画するためのものです。
差立板を見れば、その日の生産予定と進捗がわかります。
ストアは、工程からできあがった製品や部品を「かんばん」と共に、ならべて置く場所です。
「後工程」が、ここから製品や部品を引き取っていきます。
お客である「後工程」が、あたかも店先に並んでいる商品を買っていくような場所であることから、ストアと呼ばれます。
作業前品置き場は、「前工程」から引き取ってきた製品や部品を一時的に置く場所です。
今から作業するモノを投入順や担当別に置くことから、現物の差立板とも言えます。
現物による投入順や担当別の計画ができない場合は、各工程に差立板を設置することもあります。
作業前品置き場は、部品棚、部品ラックとも呼ばれます。
保管量は、1回の引き取り分プラスαとします。
工程が連結されると「前工程」のストアと一体となり、作業前品置き場は無くなります。
モノとかんばんの流れ
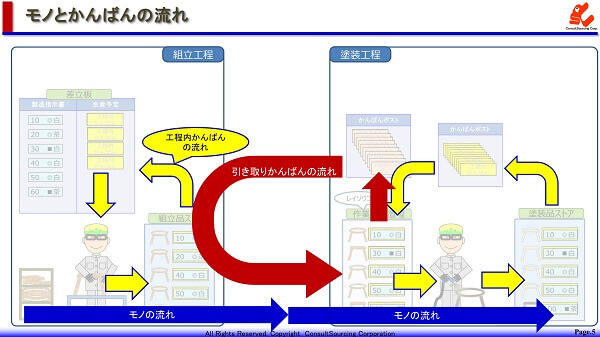
それでは、「かんばん」とモノの流れを見ていきましょう。
モノは、組立から塗装へ、ストア、作業前品置き場という順に流れていきます。
「工程内かんばん」は、ストアから外れ、かんばんポストまたは差立板、作業前品置き場へ、そして製造を経て、ストアへと流れます。
「引き取りかんばん」は、「後工程」の「かんばんポスト」から「前工程」へ送られ、ストアで「工程内かんばん」と差し替えられて、「後工程」の作業前品置き場へ流れます。
作業前品が製造に投入されると、外されて、「かんばんポスト」に入れられます。
かんばんサイクルと物流ロットサイズ
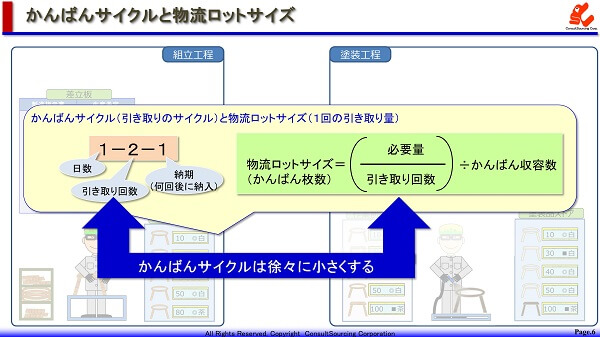
ここで、かんばんサイクルと物流ロットサイズについて整理しましょう。
かんばんサイクルとは、「後工程」が「前工程」から製品や部品を引き取るサイクルのことで、「前工程」にとっての納期となります。
通常、「引き取りかんばん」では、1の2の1というように、3つの数字で表されます。
最初の数字は、日数を示します。
引き取りサイクルのベースとなる日数になります。
何日に何回引き取るという場合の「何日」にあたるところです。
2番目の数字は、引き取り回数です。
ベースの日数内における引き取る回数です。
何日に何回引き取るという場合の「何回」にあたるところです。
外注からの引き取りでは、納品トラックの便数となります。
3番目の数字は、納期です。
「後工程」が製品や部品を引き取る時は、次にほしい製品や部品の「引き取りかんばん」を、持ってきます。
持ってきた「引き取りかんばん」の製品や部品を、何回あとの「引き取り時」にほしいと言っているのです。
1であれば、1回あと、つまり、次の引き取り時まで用意しておかなければなりません。
事例の1の2の1は、1日に2回の引き取りがあり、「引き取りかんばん」を持ってきた1回あと、つまり、次の引き取り時までに、モノを用意しなければならないことが示されています。
物流ロットサイズとは、1回に引き取る量のことです。
工程が1回に用意しなければならない数量でもあり、引き取りサイクルの納期内での生産量ということになります。
計算式は、月や週、または1日の必要量を、その期間での引き取り回数で割って求めます。
さらに、「かんばん収容数」で割ると1回の引き取りで運用する「かんばん枚数」が算出されます。
このように、「かんばんサイクル」と「物流ロットサイズ」は、密接な関係にあります。
「かんばん方式」の導入初期は、「かんばんサイクル」の日数の数値を大きくして、「物流ロットサイズ」が現在の1回の生産量と同じくらいのところから始めます。
「物流ロットサイズ」が大きいうちは、工程内の「しかかり在庫」が多く、リードタイムも長く、「かんばん方式」導入のメリットはほとんどありません。
段取り改善や平準化改善を進め、小ロットでも生産できるようになってきたら、徐々に「かんばんサイクル」を小さくして、「物流ロットサイズ」を小さくします。
工程内の「しかかり在庫」が少なくなり、リードタイムも短くなって、「かんばん方式」導入のメリットが表れ始めます。
受注型・多品種少量生産のかんばん方式の運用方法
受注型・多品種少量生産におけるかんばん方式の運用方法は以下の動画で解説します。
動画をご覧ください。
Copyright © 改善と人材育成のコンサルソーシング株式会社