Blog
7.162018
トヨタの工場管理の7つの視点~QCDSと4Mの見える化
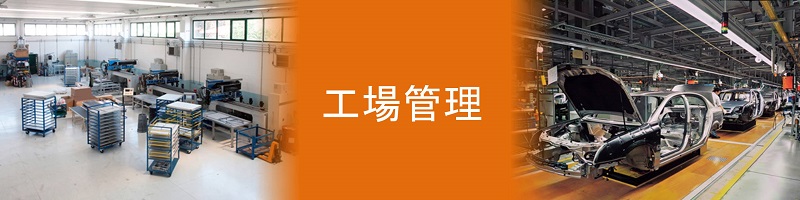
生産管理:工場長・製造管理者のため見える化の進め方・事例
トヨタ生産方式の生産管理は7つ視点で変化と異常を見える化して管理します。この7つの視点(モノ、4M、QCDS、情報、日常管理、方向性・思い、全体・経営)の定義と見えるの方法を紹介します。
<目次>
モノの見える化と管理方法
4Mの見える化と管理方法
QCDSの見える化と管理方法
情報の見える化と管理方法
日常管理の見える化と管理方法
方向性・思いの見える化と管理方法
全体・経営の見える化と管理方法
モノの見える化と管理方法
モノ(材料・製品・仕掛品・不良品・工具・治具・ゲージなど)が見えない状態では、探索・手待ち・つくり過ぎ・不良などのムダが発生します。
そこで、このようなムダを排除するために5Sを徹底させます。5Sをお掃除活動にすることなく、ハタラキヤスク(早く・正しく・楽に・安く)なるような活動にしていきます。
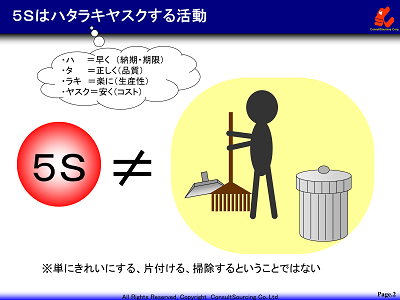
では、モノ見える化の例として、改善シートを使った整理推進事例をご紹介します。
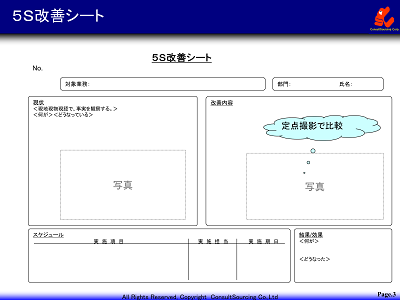
・5Sができていない箇所の現状の姿を写真に撮る。
・5S改善シートの左半分にその写真を貼り付ける。
・その写真の意味を何が、どうなっているかという補足を文章で付け加える。
・その問題に対し、改善スケジュール(実施項目・担当・期限など)を下段に記入する。
・シートをよく目に付く場所に掲示する。
・見える化されることにより問題が明らかになり、改善行動が促される。
・期限が迫ってくると、朝礼などで進行具合を管理者がチェックする。
・期限遅れに対しては、管理者ができない理由や遅れている理由を確認しサポートする。
・改善が終了したら定点(現状の写真を撮った位置)撮影し、その写真を右半分に貼り付ける。
・効果の確認を右下に記入し、5S改善シートの記入を完成させる。
・完成したシートは一定期間掲示し、その後ファイルしておく。
このように整理を推進することで、不要なものが見える化され、それに対する処置行動につながっていきます。
4Mの見える化と管理方法
4Mとは、生産に必要な要因系(インプット)のアイテムのことで、Man(人)、Machine(設備・機械)、Method(方法)、Material(原材料)を指します。これらの状況が見えないことで、人や設備に対するムリ・ムラ・ムダが発生します。
では、4Mの中でもMan(人)見える化の例として、ワークサンプリング(人の動作を瞬間的に観測し各観測項目の時間構成やその推移状況などを統計的に推測する方法)を使った動作のムダ取り推進事例をご紹介します。
ワークサンプリングの進め方は、
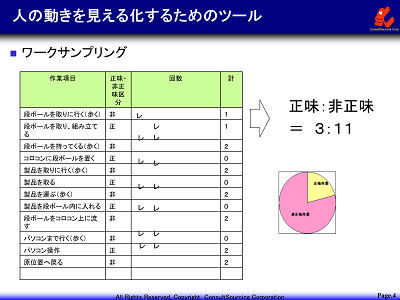
・観測する対象と範囲を決定する
・観測する作業項目を決定する
・観測回数を決める
・観測する
・観測値の集計、分析を行う
このように観測項目を層別することで正味作業と非正味作業が見える化され、非正味に焦点をあてた処置行動につながっていきます。
QCDSの見える化と管理方法
QCDSとは、製品における結果系(アウトプット)のアイテムのことで、Quality(品質)、Cost(コスト)、Delivery(納期)、Safety(安全)を指します。
これらの状況が見えないことで、不良品・原価高・納期遅延・労働災害などが発生します。
では、QCDSの中でもQuality(品質)見える化の例として、アンドン(人を機械の番人にさせることのないように異常があれば機械が止まりその異常を知らせる道具)をご紹介します。
・呼び出しアンドン;部品が無くなりそうな時に部品補充をしてもらうために「水すまし」などを呼び出すもので、呼び出し作業者の位置がランプで表示され、部品補充者は速やかに部品を補充する。
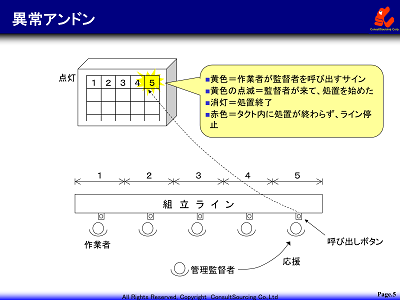
・異常アンドン;不良品の発生、工程内トラブル・設備故障などの異常が発生した時に管理監督者を呼び出すもので、管理監督者は異常に対処しラインが正常に戻るまで作業者の支援を行う。
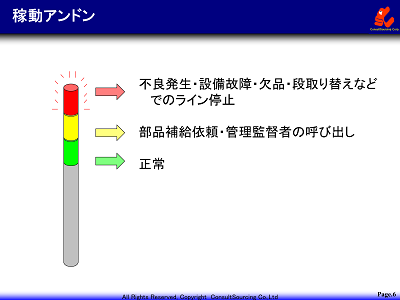
・稼動アンドン;設備の稼動状態を表すもので、赤・黄・緑色の3色で表示される。赤色=不良発生・設備故障・欠品・段取り替えなどでのライン停止、黄色=部品補給依頼や管理監督者の呼び出し、緑色=正常、などの意味で使われる。
このように設備の異常を見える化することで、人と機械の作業が分離でき、人は異常でストップした時のみ処置行動すればよくなります。
情報の見える化と管理方法
モノは、情報によってつくられます。この情報が見えなければ、7つのムダと言われるつくり過ぎのムダ・手待ちのムダ・運搬のムダ・加工そのもののムダ・在庫のムダ・動作のムダ・不良をつくるムダが発生します。
では、情報見える化の一例として、生産管理版を使った予実・進捗管理の推進事例をご紹介します。
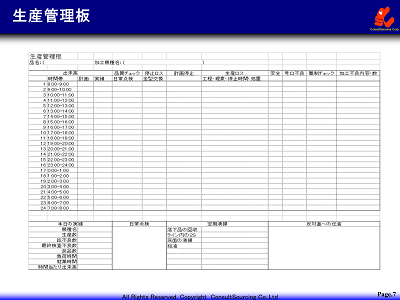
生産管理板は、
・異常を早く顕在化し、処置や改善の促進を図る
・時間ごとの生産進捗状況を把握する
・作業者に目的意識を持たせる
・タクトタイム生産する必要性を認識させる
などの目的のもと、縦軸には時間軸をとり、横軸には計画数・実績数・停止時間・不具合内容などを取り、現場に掲示します。時間軸は製品の完成時間によっても異なりますが通常は1時間単位で目盛をとり、横軸の時間あたりの管理項目の空欄に実績を作業者が記入していきます。
このようにすることで、計画数と実績数の差や時間当たり出来高のバラツキ、遅れ進みや不具合の内容・可動率の低下要因などを確認することができ、応受援などの処置行動につながっていきます。
日常管理の見える化と管理方法
日常管理は、当たり前のことを当たり前にさせることです。日常管理が疎かになると、様々なムダが発生します。
では、日常管理見える化の例として、ルールの道具化の推進事例をご紹介します。
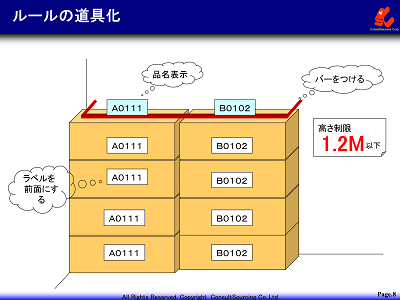
日常管理の基本は、
・K;ルールを決める
・M;ルールを守る/守らせる
・K;ルール通りに行っているか観察しできていなければ改善する というKMK活動です。
そして、決めたことを守らせるには、ルールを見せて、道具化することが肝要です。道具化とは、例えば1.2メートルの高さにバーなどの障害物をつけてそれ以上の高さにものが置けないようにしてしまうことです。
このようにすることで、決められた場所以外にモノが置かれることでそれに対する処置行動につながっていきます。
方向性・思いの見える化と管理方法
人の心や腹の中は見えません。
そこで、それが見えれば、何を考えているのか、何をしたいのか、が分かり、進むべき方向性へのシナジーや助け合いなどが生まれます。
では、方向性・思いの見える化例として、演繹的(過去からの延長戦で考える帰納法アプローチと異なり、目的をベースにして、未来の「あるべき姿」をデザインし、そこから学びながら現状を変えてゆく)アプローチの推進事例をご紹介します。
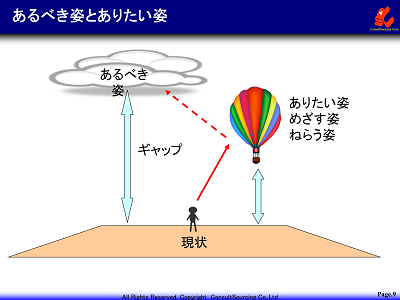
あるべき姿・ありたい姿・現状の姿を描きます。
・あるべき姿;現実では当面不可能であるがそうであったら良いなあという理想像で、すぐには手の届かないような高い目標を指す(いわゆる理想の姿)。
・ありたい姿;あるべき姿より現実的に手の届きそうな数年先に到達可能な姿で、自分たちの環境や能力などを背景として努力すれば達成できる当面の目標を指す(めざす姿・ねらう姿とも言う)。
・現状の姿;現在のありのままの姿で、現在の実力(能力)を指す。
このように3つの姿を描くことで、ギャップ(問題)が明らかになり、処置行動につながっていきます。
全体・経営の見える化と管理方法
全体が見えないと部分最適に陥ります。
では、全体見える化の一例として、モノと情報の流れ図を使った工場のボトルネック改善推進事例をご紹介します。

工場全体や物流・サプライヤーとの関連を眺めてみると、モノや情報が思わぬところで停滞していることがあります。
これら工程間におけるモノや情報の停滞は、リードタイムを長くし、在庫を膨らします。モノと情報の流れ図を作成することで、この停滞箇所をつきとめ改善し、必要なモノだけをタイミングよくつくり運ぶことができ、各工程を部分最適から全体最適に変えることができます。
このようにモノと情報の流れの現状を明らかにし、ありたい姿(ねらう姿・めざす姿)を描くことでギャップが明らかになり、流れを阻害している箇所への処置行動につながっていきます。
生産管理・現場改善についての研修・診断・コンサルティングの個別相談・お問い合わせ![]() ![]() |
トヨタ生産方式の改善に役立つツール・帳票
トヨタ生産方式のムダとり、見える化、平準化など様々な管理や改善に役立つ実践ツールや帳票を多数公開中!
ツール使い方や管理・改善手法も動画で解説しています。公開ページはこちら⇒「クリック」
Copyright © 改善と人材育成のコンサルソーシング株式会社