Blog
9.252018
生産計画の立て方と所要量計算・基準在庫の設定の仕方

売れるスピードにつくるスピードを追随させる生産計画と手配の仕方
生産計画の目的は、売れるスピードに追随できる生産体制の準備にあります。生産手配の目的は、生産能力の準備と資材の調達です。最小の在庫で欠品なく効率よく生産するために、需要予測と販売計画から生産計画を立案し、部品展開で資材所要量を算出し、必要な生産能力の準備し、生産計画通りの生産をするためのリソースを手配する、生産計画の立て方と手配の仕方を紹介します。
<目次>
生産管理とは
売れるスピードにつくるスピードを追随させる
・つくるスピードを変える方法
・売れるスピードを平準化させる方法
・スピード差を埋める適正在庫
生産計画のやり方と事例
・需要予測・販売計画から長期生産計画の立て方
・生産計画に基づいて4Mを計画し準備する
生産手配のやり方と事例
・必要工数を算出して生産能力を準備する
・生産順序計画では毎日投入にする
・生産順を日程計画に展開
・所要量計算(MRP)と発注数の算出
・基準在庫の設定
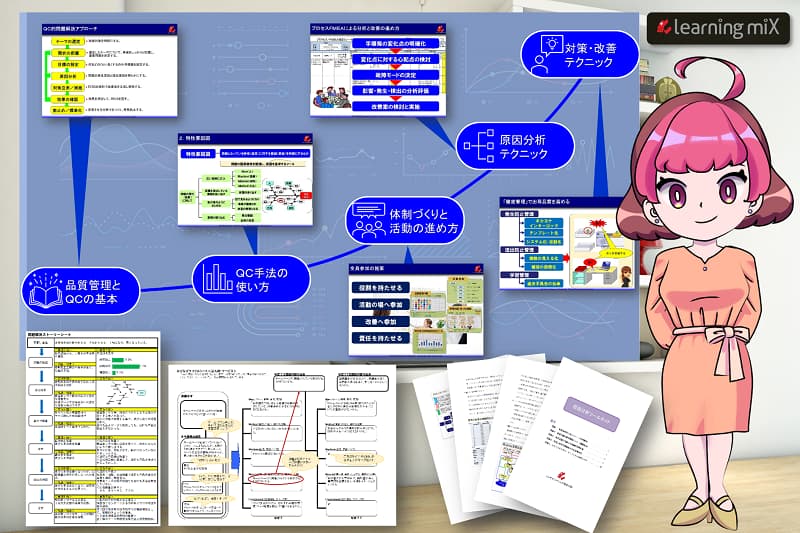
生産計画の立て方と所要量計算
生産管理とは
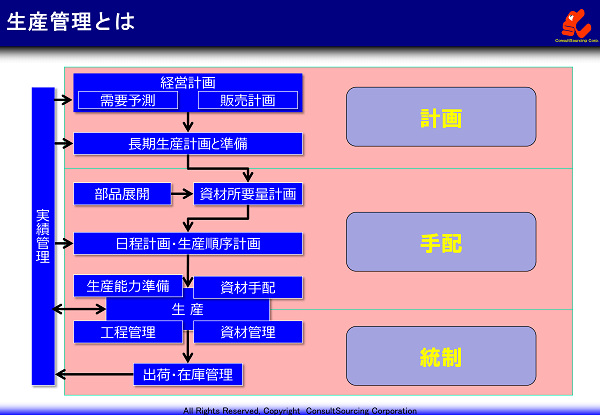
生産管理とは、顧客ニーズを把握して、需要を予測し生産計画を立て、購入・外注の手配をし、計画通りに進行するよう統制することです。
具体的には、まず会社のビジョンや戦略が構築され、経営計画に落とされます。
その経営計画に従い、需要予測と販売計画が立てられ、長期生産計画が、立案されます。
長期生産計画は、大日程とも呼ばれ、大まかな計画ですので、そこから更に、中日程や小日程の生産計画に落とされます。
生産財のメーカーでは、顧客の内示情報が長期生産計画となり、確定情報が生産計画となります。
次に、部品展開から資材・部品の所要量を計画し、在庫状況を捉えます。
生産能力の準備と確保を行い、日程計画・生産順序計画、資材手配が行われて、生産されます。
生産では、工程の進捗状況と資材の手配入荷状況、製品の在庫や出荷状況を監視し、異常を検知して、正常に戻すための処置を行います。
生産や在庫、出荷の実績データを収集し、計画や手配へとフィードバックして計画精度、手配精度を高めるPDCAサイクルを回します。
このように生産管理は、大きく分けると、計画、手配、統制という3つの柱から構成されます。
生産管理の目的
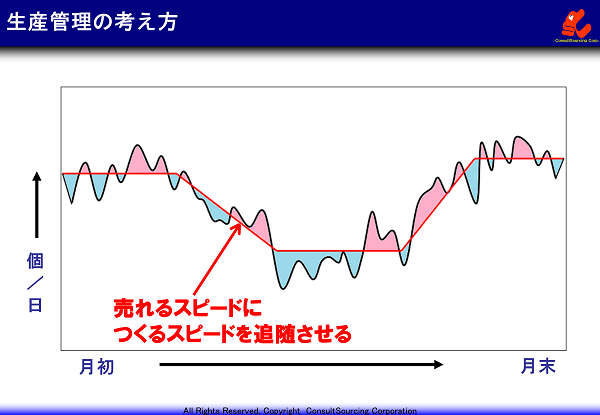
では、生産管理の目的とは、何でしょうか。
売れるスピードは、常に変化しますが、つくるスピードを固定化したままでは、在庫や欠品が多発します。
在庫や欠品を減らすには、売れるスピードにつくるスピードが追随できるようにしなければなりません。
つまり、生産管理とは、売れるスピードにつくるスピードを追随させることです。
売れるスピードにつくるスピードを追随させる
では、売れるスピードにつくるスピードを追随させるにはどうすればよいのでしょうか。
追随させる方法は、2つあります。
つくるスピードを変える方法
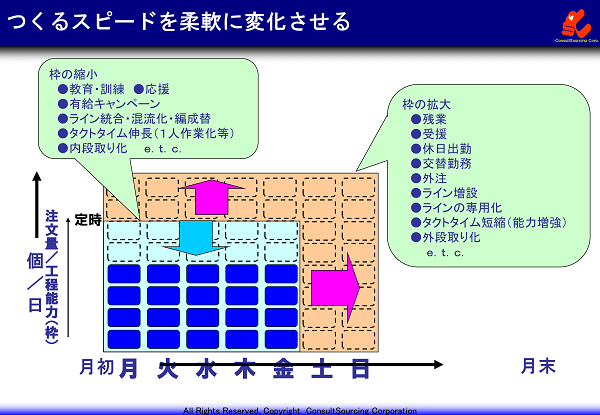
1つ目は、つくるスピードを変える方法です。
工程の生産能力の大きさ、つまり能力枠を大きくしたり、小さくしたりすることで、1日に生産できる量を変動させる方法です。
小さくするには、教育・訓練、応援、有給消化、ライン統合、混流化、編成替、タクトタイム伸長、内段取り化などをします。
ライン統合、混流化、編成替、タクトタイム伸長、内段取り化などは、大きく変えることができますが、時間がかかる取り組みですから、中長期的な生産計画に基づいて行います。
大きくするときは、残業、受援、休日出勤、交替勤務、外注化、ライン増設、ライン専用化、タクトタイム短縮、外段取り化などをします。
同様に外注化、ライン増設、ライン専用化、タクトタイム短縮、外段取り化は、中長期の生産計画に基づいて行います。
売れるスピードを平準化させる方法
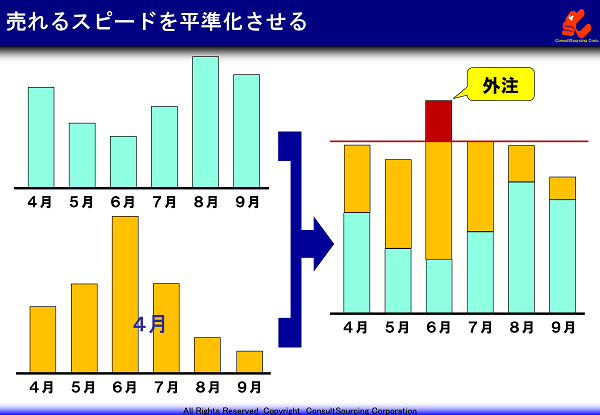
2つ目は、売れるスピードを平準化する方法です。
平準化とは、変動の幅を小さくすることです。
売れるスピードは、市場によって決まりますから、自由にコントロールすることはできません。
そこで、売れるスピードの異なる2つ以上の製品を組み合わせることで、トータルの売れるスピードの変動幅を小さくします。
変動幅が小さくなれば、つくるスピードは追随しやすくなります。
具体的には、1つのラインで複数の製品を生産する混流ラインの構築やラインの統合、編成の組み替えなどを行います。。
それでも、変動幅が大きく、つくるスピードが追随できない場合は、飛び出た部分を外注に依頼することで、社内で対応する範囲の変動幅を小さくします。
在庫を積みますことになりますが、生産を前倒しすることで、生産しなければならない量を平準化する方法もあります。
これは、一時的に安全在庫を増やす方法となります。
スピード差を埋める適正在庫
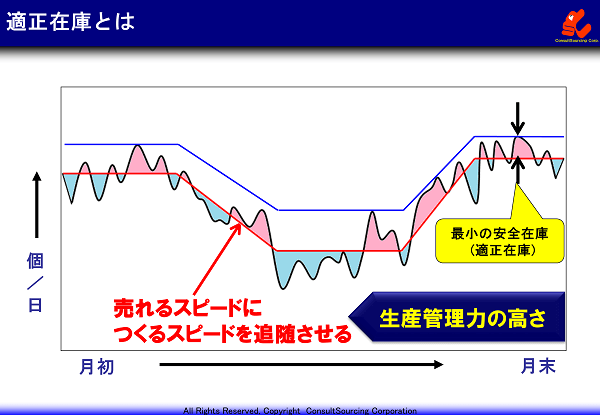
あらためて在庫の意義について考えてみましょう。
売れるスピードの激しい変化に対し、つくるスピードの柔軟性を高めたとしても、完全に追従することはできません。
売れるスピードの変化には、数日から数ヶ月にわたる大きいうねりのような変化と、日々の細かな変化があります。
つくるスピードは、生産体制を変えて対応するため、大きなうねりには追随させることができても、日々の細かな変化に追随することはできません。
また、突発的な変化にも対応できません。
そこで、日々の細かな変化や突発的な変化による欠品を防ぐために、最小の安全在庫を持ちます。
この最小の安全在庫が、適正在庫となります。
売れるスピードに、つくるスピードをどのくらい追随させることができているかが、生産管理力の高さとなります。
生産管理力の高い工場では、安全在庫は小さくなります。
生産管理力が低い工場は、売れるスピードに、つくるスピードが追随できていないので、在庫への依存度が高くなり、安全在庫は大きくなります。
生産計画のやり方と事例
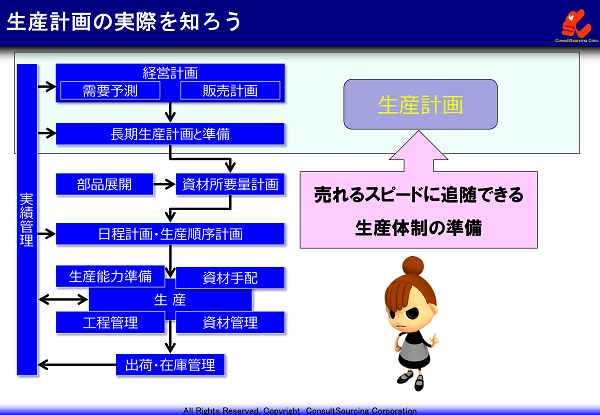
それでは、生産計画は、どのように行われるのかをみていきましょう。
生産計画の目的は、売れるスピードに追随できる生産体制の準備にあります。
需要予測・販売計画から長期生産計画の立て方
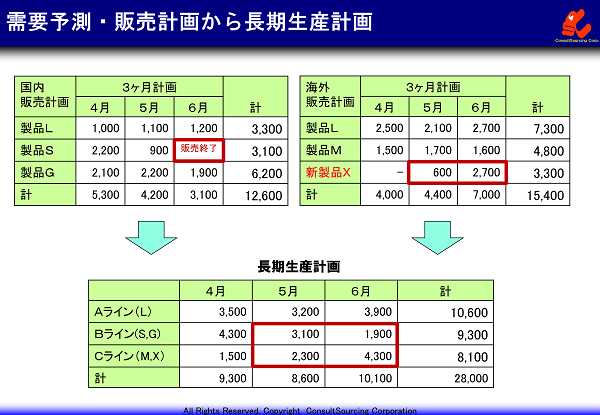
経営計画や需要予想、顧客からの内示情報などに基づいて、販売計画を立て、その販売計画に基づいて、数ヶ月から1年の長期生産計画を立案します。
ラインや設備の新設や改造など、投資に関わる場合は、1年程度の見通しを立てます。既存ラインなどの生産管理では、3ヶ月程度の見通しで生産計画を立てます。
販売の終了する製品がある場合や新製品の立ち上げなど、販売量、生産量が大きく変動するタイミングと量などを明らかにして、その対応計画を立てて準備します。
事例の場合、5月から新製品が立ち上がり、と6月に販売終了のなる製品があります。
そのため、Bラインは5月から生産量が減り、Cラインは逆に生産量が増加します。
この2つのラインは生産量の変動が大きいことがわかります。
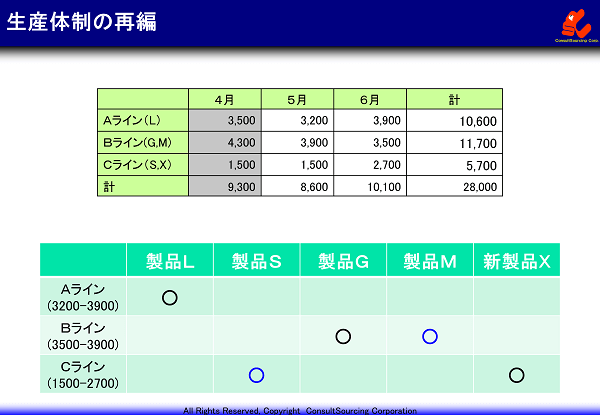
そこで、各ラインの生産アイテムの組み合わせを変えて、変動幅を小さくする生産体制を考えます。
製品SはCラインへ移管し、製品MはBラインへ移管します。
これによって、Bラインの生産量の変動幅は小さくなり、生産管理がしやすくなります。
Cラインは、実質、新製品Xの専用ラインとなります。
新製品の立ち上がりトラブルが他製品へ影響しなくなり、生産管理上のリスクが軽減できます。
生産計画に基づいて4Mを計画し準備する
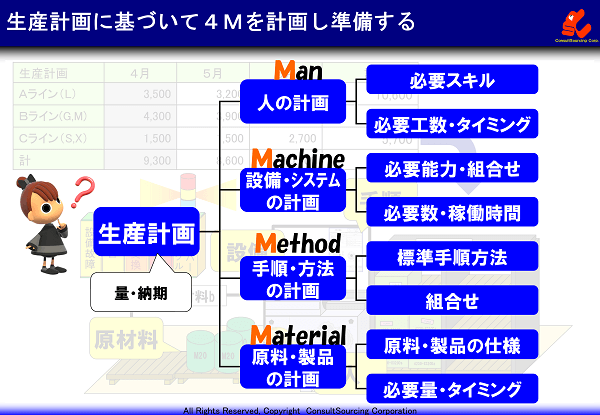
生産計画が立案されたら、ラインで生産するために必要なリソースを計画し、準備します。
リソースとは、人、設備、手順、原材料のことを指し、4Mと言います。
人の計画では、必要とするスキルや工数、必要となるタイミングを明らかにし、準備します。
設備・システムの計画では、必要とするラインや設備、システムの構成と能力、組み合わせ、数量、時間を計画し、準備します。
手順・方法の計画では、加工や組み立て、運搬のための標準手順や操作方法、工程や作業の順番、組み合わせなどを計画し、準備します。
原材料や部品、半製品の計画では、必要となる原材料、部品などの規格や仕様、数量、必要となるタイミングを計画し、準備します。
これら4Mを計画し、生産体制を整えることが生産計画を立てる目的です。
※生産管理では、計画し準備した4Mを適切に維持管理することが求められます。
4Mの維持管理については以下の記事を参照ください。
生産手配のやり方と事例
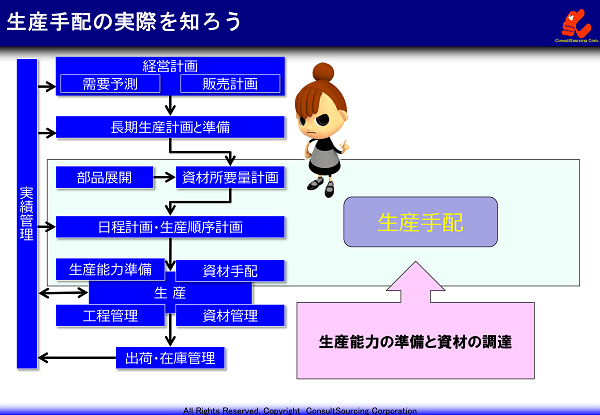
続いて、生産手配は、どのように行われるのかをみていきましょう。
生産手配の目的は、生産能力の準備と資材の調達です。
必要工数を算出して生産能力を準備する
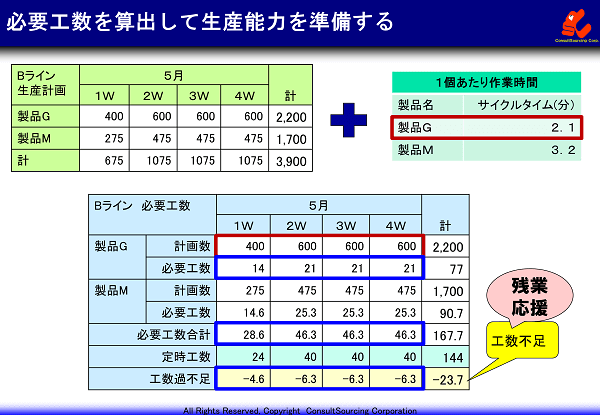
生産能力の準備とは、計画された数の生産を行うための作業者の必要工数を算出して準備することです。
準備は、作業者の確保、勤務日数や時間の調整などを行います。
同様に、使用する設備の必要稼働時間を算出し、準備します。
使用する設備の確保、操業時間の調整などを行います。
ここでは、作業者の必要工数の算出を事例に説明します。
設備の稼働時間の計算方法は、人の工数の計算方法と同じですから、参考にしてください。
生産計画で立てられた製品毎の生産数を週単位の生産数に展開します。
事例は、5月の計画ですから、1週目はゴールデンウィークで出勤日数が少ないことから生産数を他の週より減らしています。
このように休日やイベントなどを考慮して週ごとの生産数を決めていきます。
このあと、算出された必要工数から生産数を再調整することもあります。
週ごとの生産数と製品1個あたりの作業時間から必要工数を算出します。
製品1個あたりの作業時間は、標準作業から決められた標準時間を使うのが理想ですが、実際には、過去の生産実績の生産数を総作業時間で割って求めた値を使うことが多いです。
具体的には、週ごとの生産計画数と1個あたりの作業時間のサイクルタイムをかけて、週ごとの必要工数を算出します。
すべての製品の必要工数を算出して、週ごとの必要工数の合計を求めます。
定時の工数との差から、工数の過不足を求めます。
工数が不足しているところは、残業や応援などを計画して準備します。
生産順序計画では毎日投入にする
生産順序計画は、ラインに投入する製品の生産順番を決めることです。
1ラインで複数製品を生産する場合の製品毎のつくる順番のことです。
1ライン1製品の場合は、生産順序計画は必要ありません。
生産効率優先の投入順
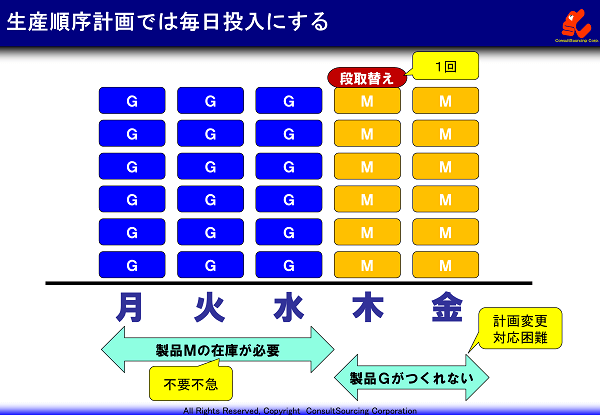
多くの場合、生産効率を考えて、段取り回数が少なくなるように生産順番を考えます。
事例は、月曜から水曜日まで製品Gを生産し、木曜日から製品Mを生産する計画となっています。
この場合、木曜日に製品Mの生産に切り替えるための段取りを1回、行うだけです。
このような投入順では、月曜から水曜日まで製品Mは生産しないので、その間の出荷をカバーするだけの在庫が必要となります。
同様に、製品Gは木曜と金曜は生産できないので、在庫が必要となります。
在庫は、つくれない期間の出荷を見込んで生産しますから、多めに、不要不急なものまでつくることになります。
もし、つくれない期間に販売数の計画変更が発生しても、そのための生産数の変更調整は困難です。
このような変更調整できなかった経験すると、人は、さらに安全をみて、多めに生産したくなります。これが、在庫を増加させる理由です。
では、どうすればよいでしょうか。
変更への柔軟対応優先の投入順
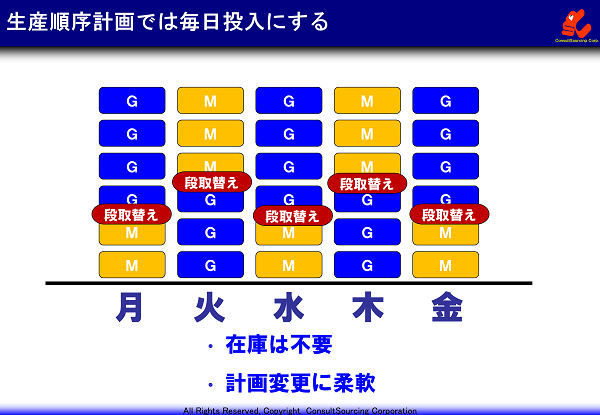
生産順序計画では、そのラインで生産する製品を毎日投入するようにしましょう。
当然、段取り回数は毎日となり、5倍になります。生産性は一旦、落ちます。
しかし、改善すれば、生産性に問題ないレベルにすることができます。
毎日投入のメリットは、在庫が必要ないことです。
不要不急の在庫をつくることに時間もお金もかけなくてすみます。
毎日、生産しているので、計画変更に対しても柔軟に対応できます。
見込み生産ではないので、今日、必要なモノを、今日、つくっていますから、販売数が変更されても製品の生産の終了と次の製品の生産開始時間を変えるだけで対応できてしまうのです。
生産順序計画では、段取りのロスを恐れず、毎日投入で変更や突発対応への柔軟性を高めることをめざしましょう。
生産順を日程計画に展開
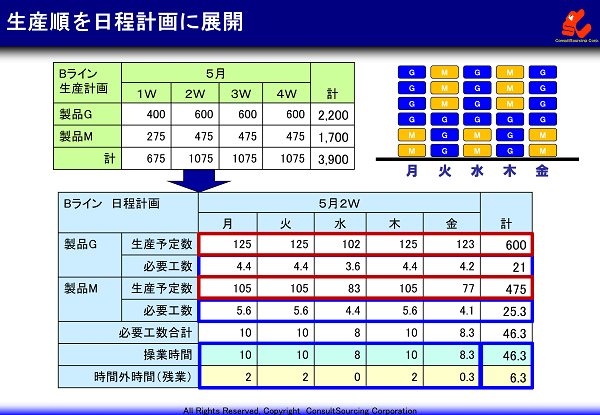
続いて、ライン別・製品別生産計画を生産順序計画に基づいて、日程計画に展開します。
生産能力準備の段階で、必要工数の過不足はわかっていますから、そこから日々の操業時間の予定を立てます。
具体的には、定時の日と残業をする日の設定です。
事例は、水曜日を定時の日とし、月曜、火曜、木曜を2時間残業としました。金曜日は、端数の時間を残業します。
実際には、トラブルや注文数の変動がありますので、金曜は、その対応の余力を残しておくように考えました。
日々の操業時間が決まったら、製品別の必要工数の割り振りをします。
計画された生産数を生産できるように時間と数量の調整をして生産予定数の割り振りをしていきます。
所要量計算(MRP)と発注数の算出
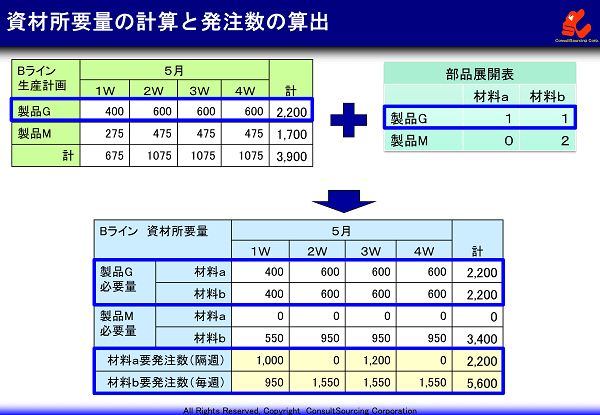
続いて、資材所要量計画(MRP)です。
製品別生産計画と部品展開表から、製品ごとの必要となる材料の数量を算出します。
部品展開表は、製品ごとに使用する材料や部品の使用量を明確にしたものです。
製品別生産計画にある製品の生産数に部品展開の使用量をかけて、製品別の材料の必要量を算出します。
必要量が決まったら、発注数を算出します。
発注サイクル、入荷サイクルを加味して、必要量を満たす発注数を決めます。
事例では、材料aが隔週の発注のため、2週分の必要数を合算して発注数を決めています。
計画段階では、生産計画数から必要量を算出し、発注数を決めていますが、実際の手配段階では、実際の生産数や使用数、歩留まり、安全在庫数も加味して、発注数を発注の都度決めていきます。
基準在庫の設定
最後は、基準在庫の設定です。
在庫は、出荷数または資材在庫数の変動による欠品を防止する役割があります。
生産管理では、基準在庫を設定し、それを下回らないように生産数や発注数の調整をします。
製品の在庫基準の設定方法
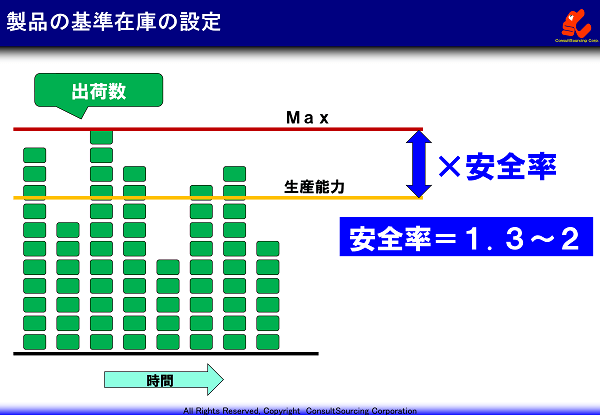
製品の基準在庫は、出荷数または注文数の最大値と生産能力の差に安全率をかけたものとなります。
安全率は、将来の大きな変動や突発的なトラブルに対応するためのバッファを確保することが目的です。
掛け率は、変動や突発のリスクの大きさによって変わりますが、1.3倍から2倍とすることが多いようです。
資材の在庫基準の設定方法
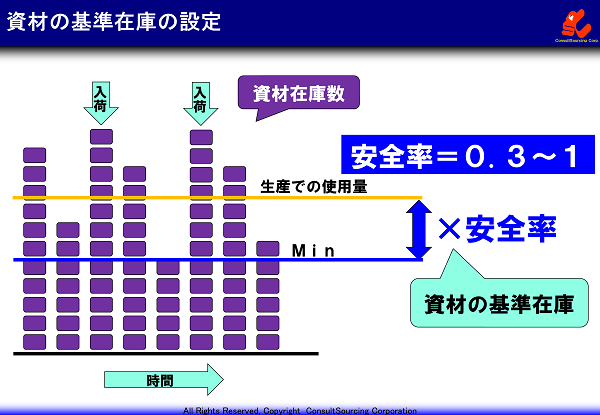
生産で使う材料や部品などの資材は、入荷と入荷の間で在庫が消費され、入荷直前に在庫が最も少なくなります。
最も少なくなったときに欠品しないようにしなければなりません。
資材の基準在庫は、資材在庫数の最小値と生産での平均使用量の差に安全率をかけたものです。
安全率は、製品の基準在庫の考え方と同じです。
掛け率は、0.3倍から1倍とすることが多いようです。
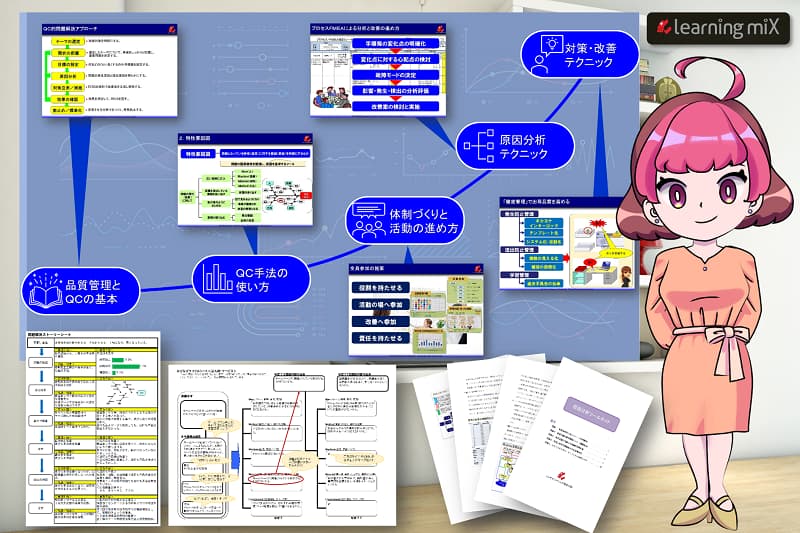
生産計画の立て方と所要量計算
Copyright © 改善と人材育成のコンサルソーシング株式会社