Blog
7.162018
生産管理力を高めるトヨタ流の変化点管理とは~進め方と事例・ツール
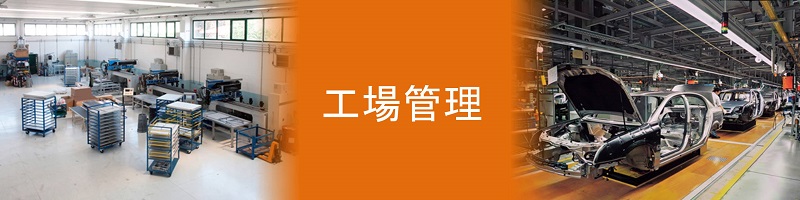
変化・変更を見える化するトヨタ流の生産管理のポイント
生産では、常に様々な変化が起きています。
生産を正常な状態に維持管理するためには、この「変化」を管理しなければなりません。
トヨタ生産方式では、この変化を管理することを変化点管理、または変更管理と言います。
生産活動における変化を適切に管理し、正常な状態に維持管理する進め方とツールについて事例を交えて説明します。
<目次>
変化点とは
変化点管理とは
変化点を見える化する
品質確認情報を見える化する
飛び込み情報を見える化する
納期変更情報を見える化する
原材料入荷変更情報を見える化する
注文変化傾向情報を見える化する
注文変更数情報を見える化する
計画・転換情報を見える化する
出荷変更情報を見える化する
変更アイテムを見える化する
変化点とは
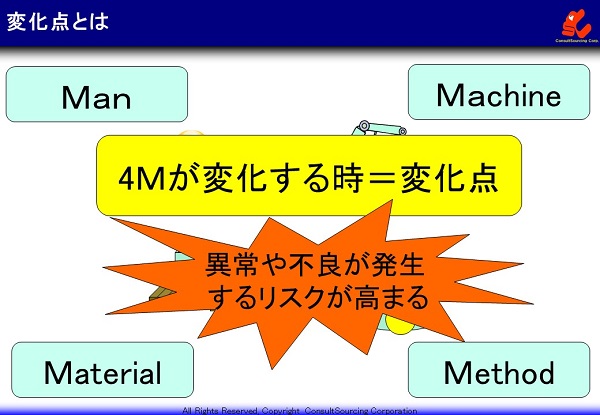
生産管理では計画が立案され、生産に移行されますが、それらは、あくまでも計画であり、生産が実際に開始されると、様々な変更が入り、計画通りに進まないことが生じてきます。
このような変更を見逃したり、伝達漏れしたりすると、QCDSに多大な損失を発生させることが起こりかねません。
変更は、製品にまつわる変化だけでなく、4Mと言われる製品をつくる環境やリソースが変化することもあります。
このような変更を、変化点と呼んでいます。
変化点とは、例えば、
1.昼夜交代勤務など作業者が入れ替わる時、担当作業者が休んで代理の者が入る時、不慣れな作業者が教育で入る時、など人/Manが変わる時。
2.設備を入れ替える時、メンテナンスをするために機械を停止させ再稼働する時、など設備/Machineが変わる時。
3.品種が切り替わる時、ロットが切り替わる時、など原材料/Materialが変わる時。
4.治具が交換される時、作業手順が変更される時、など方法/Methodが変わる時。
など、今まで流れていた作業が一時停止し、変更を生じた上で、再始動する時を指します。
このようなMan、Machine、Material、Method の変化点においては、異常や不具合の発生する確率が非常に高くなりますので、変更情報を見える化し、管理を徹底します。
変化点管理とは
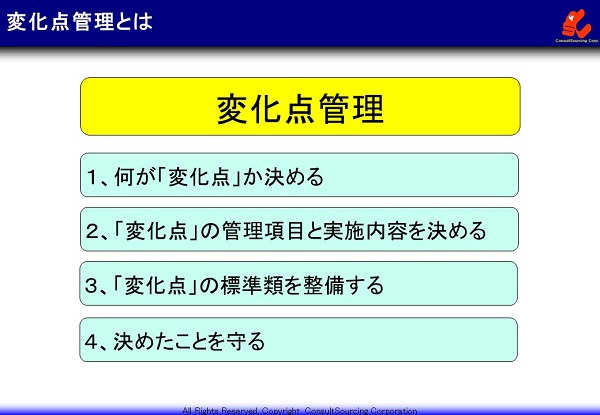
生産管理における工程の管理には、日常管理と変化点管理があります。
日常管理とは、維持の管理であり、ルールや標準を決めて守らせることです。
ですから、ラインが一旦流れてしまえば、異常がない限り、何もしなくて済むようにしていきます。
一方、変化点管理は、4Mの変化点をウォッチし、異常が出ていないか常にチェックしていきます。
変化点管理のステップは、
1.何が「変化点」か決める。
4Mの中から具体的な変更項目を洗い出し、変化点とします。
2.「変化点」の管理項目と実施内容を決める。
QCDSを担保するための管理方法を具体的にします。
3.「変化点」の標準類を整備する。
変更があった時に、誰でもできるように文書や道具を作り込みます。
4.決めたことを守る。
決めたことを守り、徹底させます。
変化点を見える化する
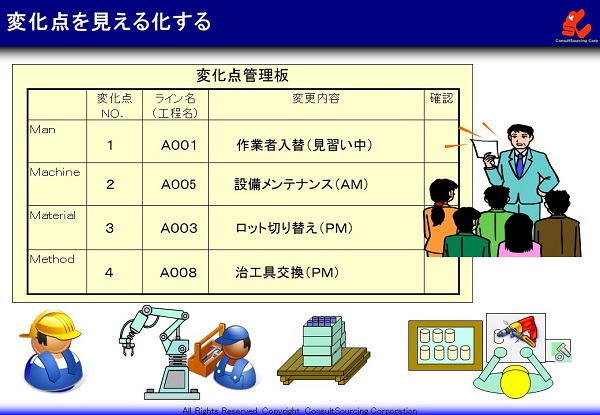
変化点は、常にウォッチし、管理するものなので、今、誰が、どこが、何が、変化点なのかという生産変更情報を、見える化します。
見える化のメリットは、担当者や担当部門以外に変更情報を共有することにあります。
モノづくりは、設計・開発、資材調達、生産管理、製造現場、生産技術、構内物流、出荷、営業など様々な部門の連携により生まれます。
そこで、変化点管理板を各職場からよく見える位置に掲示し、変更内容を記入します。
本例の変化点管理板は、縦軸に4Mを取り、横軸に変化点ナンバー、ライン名、変更内容、確認欄を設けました。
例えば、今日は、
1.Manでは、見習いの作業者入れ替え。
2.Machineでは、メンテナンス。
3.Materialでは、ロット切り替え。
4.Methodでは、治具交換。
というように、ホワイトボードなどを用いて、見える化します。
更に、朝礼などで、変更内容を伝達し、各担当に確認することで、変化点を重点管理します。
品質確認情報を見える化する
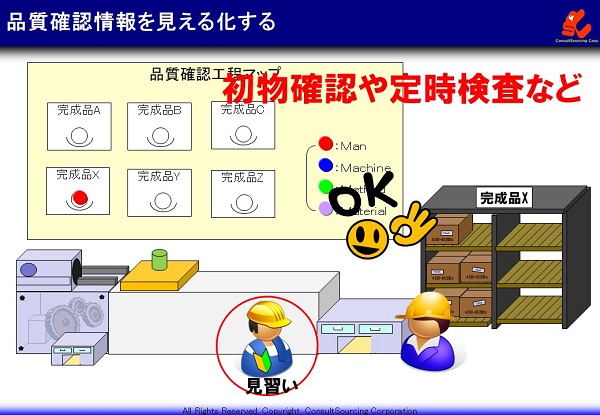
変化点を見えるようにするだけでなく、管理項目や実施内容も明らかにします。
変更により特に注意すべき点は、品質劣化や不良発生です。
そこで、品質を担保するために、品質確認工程マップをつくります。
マップには、4Mの変化点を色別のマグネットにし、対象工程に貼り付けます。
例えば、Manで完成品Xの生産ラインに見習いの作業者入れ替えがあった時、赤色のマグネットで見える化します。
このように変化点を明確にし、発生する可能性のある問題に対して、初物確認を徹底し、定時検査の頻度を増やすなど、経験者がチェックすることでミス流出を予防します。
飛び込み情報を見える化する
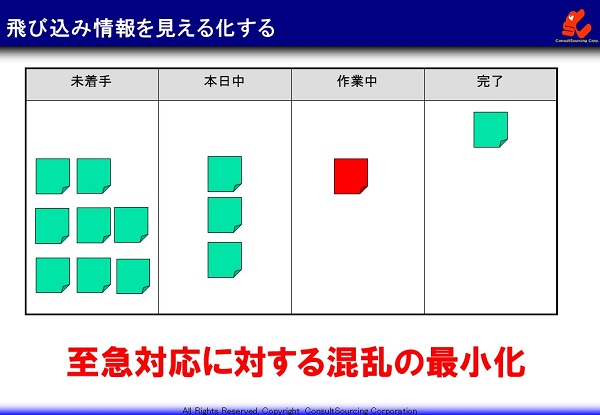
モノは、指示命令という情報から生まれます。
情報が混乱すれば、現場のモノづくりは更に混乱します。
そこで、飛び込み情報を見える化し、混乱を抑制します。
例えば、横軸に未着手、本日中、作業中、完了という欄を設け、作業内容や生産指示をカードにし、貼り出します。
未着手欄のカードから本日中にすべき作業を隣の欄に移動させ、時系列に並べます。
そこから順に作業中の欄にカードを移しながら作業を進めていき、終われば完了欄に移します。
2枚目のカードの作業に取り掛かろうとしたところで、急に飛び込み作業が入った場合、そのカードを元の位置に戻し、赤色の飛び込みカードをつくり、作業中欄に入れて作業します。
飛び込み作業が見える化されることで、影響を受ける後工程も状況把握が可能となり、混乱が最小化されます。
差し立て板で飛び込み情報を見える化する
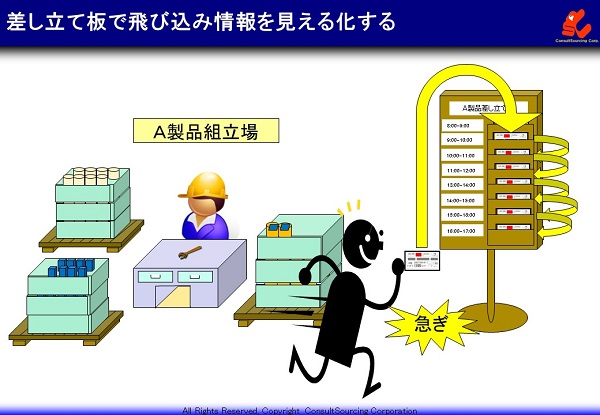
先ほどのカードで見える化したものと同様の使い方をするものとして、差し立て板があります。
差し立て板は、時間軸にカードを入れ、上から順番にカードを取りながら作業をしていきます。
作業者は、カードを順に取りながら作業すればよく、順序を決めたり、材料や収容箱の準備をするのは、ライン・リーダーや監督者の役割です。
飛び込み作業が入った場合、ライン・リーダーは、差し立て板のカードの生産順序を入れ替えます。
順序が変われば、投入側の材料供給や搬出側の完成品収容箱の引取りなどの情報も混乱するので、ライン外者は、差し立て板を見ながら段取り変更をしていきます。
納期変更情報を見える化する
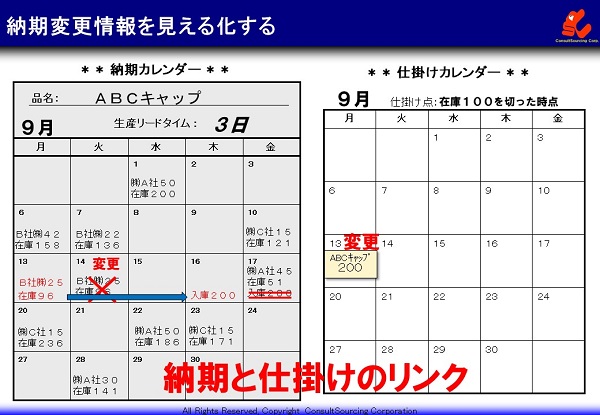
顧客の納期変更が生じれば、Manの手配、Machineの調整、Materialの調達などに混乱が生まれます。
そこで、納期と生産の仕掛けを見える化し、変更切り替えポイントを周知させます。
例えば、納期カレンダーにABCキャップ製品の納期と在庫を見える化します。
社名と数量をカードにし、移動が容易になるようにすることもできます。
納期を管理するのは、営業や出荷部門の役割となりますが、それを満たすためには生産部門も変更に対応しなければなりません。
そこで、仕掛けカレンダーをつくります。
本例では、生産リードタイムは3日かかり、仕掛け点を在庫100を切った時点としました。
計画通りならば、14日に在庫が100を切るので14日に仕掛ければ、3日後の17日に生産数量200個の入庫が加わります。
さて、それでは納期変更情報を見える化してみましょう。
14日B社25が、13日に納期変更になりました。
納期カレンダーにて、納期を変更するとともに、基準在庫として生産するタイミングも1日早めなければなりません。
そこで、仕掛けカレンダーのカードを13日に移動させ、Manの手配、Machineの調整、Materialの調達を関連部署と共有します。
このように納期と仕掛けのリンクで、4Mの変更管理が見える化されます。
原材料入荷変更情報を見える化する
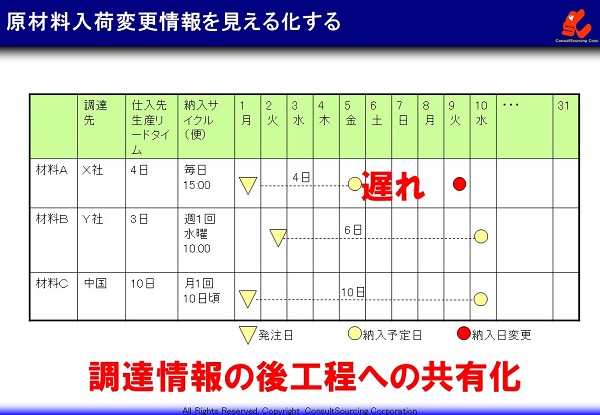
Materialの変更情報を調達部門しか把握していなければ、生産開始時に材料がなく、つくれないという状況が生まれます。
そこで、原材料入荷変更情報を見える化します。
例えば、縦軸に材料名、横軸に調達先、仕入先生産リードタイム、納入サイクル、日付と取ります。
材料Aであれば、X社からリードタイム4日で毎日届いており、1日に発注した時、4日後の5日に納入されます。
材料Bであれば、Y社からリードタイム3日で週1回届いており、2日に発注した時、便がないので6日後の10日にしか入らないことになります。
材料Cは、調達先が中国になりますので、月1回しか便がなく、発注のタイミングにより1か月以上待たされることも生じます。
このような中、入荷の遅れが生じれば、1週間とか1か月間、生産に支障をきたすことになります。
そこで、遅れの情報を日程欄に見える化し、生産部門など後工程への共有化を図ります。
調達変更情報を共有できることにより、生産順序の変更や顧客との納期調整など事前に手を打つことが可能となります。
注文変化傾向情報を見える化する
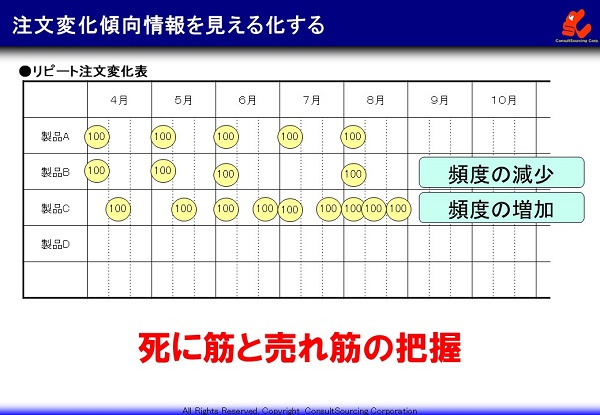
注文は変化していてもなかなか気づきません。
営業部門は把握していても生産部門に変化が伝わらず、余分な生産能力を確保してしまったり、不足する生産能力で需要に応えられないことも起こります。
そこで、リピート製品における注文傾向変化表をつくり、注文インターバルを見える化します。
例えば、縦軸に製品、横軸に時間軸を取ります。
製品Aでは、4月上旬に100個、5月に100個、というように、注文ごとにシールなどを貼っていきます。
製品Bでは、4、5、6月と100個ずつ注文が来ていたが、7月はなく、8月にまた来たというように間隔があけば、頻度の減少傾向がつかめます。
製品Cでは、4、5月と100個ずつの注文が6月以降、月2回くるようになり、頻度が増加傾向にあることがつかめます。
このように頻度の増減をつかむことは、死に筋と売れ筋の把握をすることになります。
死に筋であれば、今後生産能力を縮小していき、逆に、売れ筋であれば、生産能力を拡大していくことを、変化から予測することができます。
注文変更数情報を見える化する
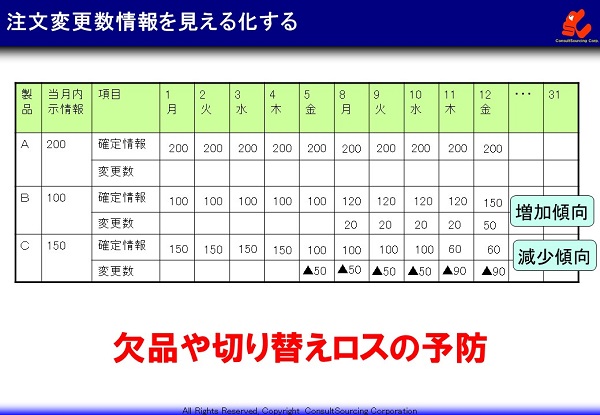
先ほどの例では、インターバルを見える化しましたが、本例は、数量の変更を見える化します。
生産財メーカーが顧客であると、通常内示情報として、翌月の注文数が予め通告されます。
例えば、製品Aは、200個、Bは100個、Cは150個というような内示情報となります。
しかしながら、これはあくまで予定であり、実際は売れの状況に応じて、上下します。
このあたりの変化をつかんでおかないと、売れ筋製品の急な増産依頼や死に筋製品の突然の打ち切りや切り替えなどにより、欠品が発生したり、廃盤となる製品在庫や材料を抱え込んでしまったりします。
そこで、確定情報を見える化し、数量の変化をつかむようにします。
例えば、横軸に日付を取り、各製品の確定情報と変更数を記入していきます。
こうすることで、Bは徐々に変更数が増加傾向にあり、売れ行きが延びだしていることがわかります。
逆に、Cは、変更数が減少傾向にあり、売れ行きが落ちていることがわかります。
このようにオンタイムで受注状況を見える化することで、ある程度顧客からの増産要請や廃盤タイミングを予測することができるようになり、欠品や切り替えロスが予防できます。
計画・転換情報を見える化する
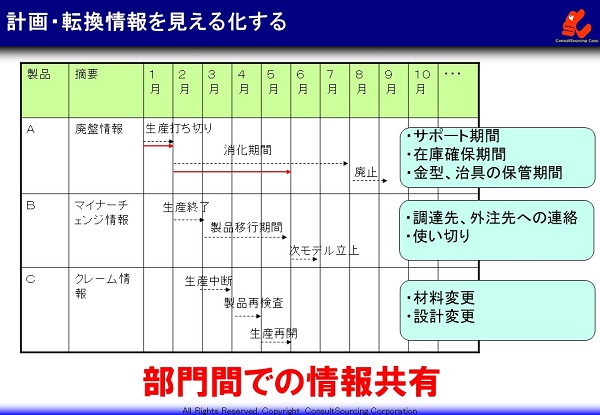
減少傾向の予測とともに、計画・転換情報を見える化します。
計画・転換情報とは、製品の廃盤情報、マイナーチェンジ情報、クレーム情報などです。
例えば、製品Aは、計画では1月に生産打ち切りとなり、7月まで消化期間があり、9月に廃止となります。
それに伴いサポート期間、在庫保管期間、金型・治具の保管期間はどうするのか、明確にしなければなりません。
また、その計画が予定より短縮されたり、延長されたりすることもあるので、赤の実践などで変更を見える化し、管理します。
製品Bは、マイナーチェンジ情報です。
生産終了、製品移行期間を経て、次のモデル立ち上げとなります。
この情報が営業部門だけなどにしか伝わっていないと、調達先や外注先への連絡が遅れ、不要な資材を購入することになってしまったり、使い切りができずに、滞留在庫を発生させたりしてしまいます。
製品Cは、クレーム情報です。
重大なクレームが発生すると、生産が中断され、製品再検査が行われ、対策が施されれば、生産再開となります。
クレーム対策として、材料変更や設計変更が必要になることも出てきますので、予め関係部署にこのようなクレーム情報を共有し、状況の推移が見える化されるようにします。
このように部門間で情報共有する仕組みがロスを最小限に抑えることにつながります。
出荷変更情報を見える化する
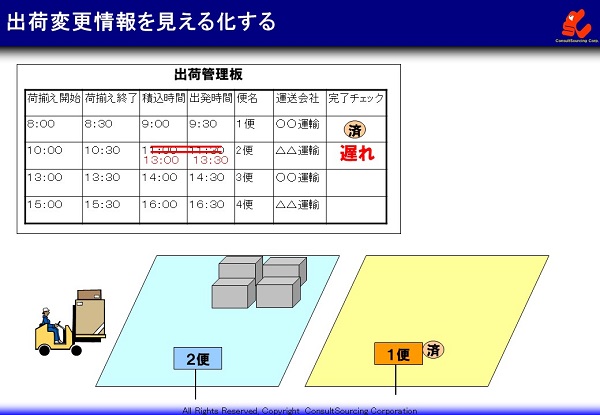
工場の入り口であるMaterialの変更情報の見える化のしかけは先にご説明しましたが、出口の出荷場の変更情報の見える化も大切です。
例えば、出荷管理板で見える化を行ないます。
出荷管理板には、横軸に、荷揃え開始、荷揃え終了、積み込み時間、出発時間、便名、運送会社、完了チェックなどを取り、縦軸で便数を管理します。
例えば、2便のトラックが渋滞に巻き込まれ遅れが生じた場合、その情報を出荷管理板上で変更し、構内物流の運搬者や顧客の営業担当などが分かるようにし、処置を行います。
変更アイテムを見える化する
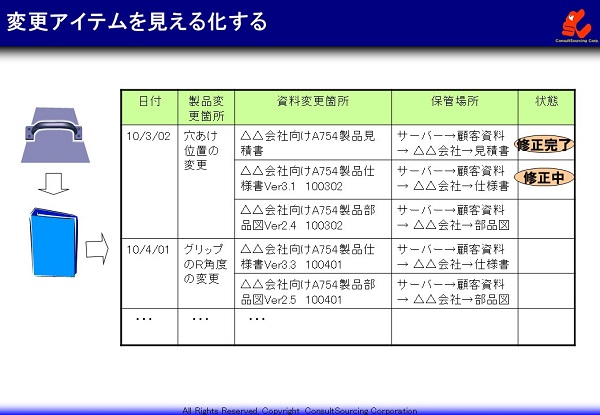
変更管理で最後に大切なことは、トレーサビリティです。
変更された製品が追跡できるようにし、再検査の範囲やリコール対象を特定することができるようにしなければなりません。
そのためには、4Mが変化した時点を確実に追えるようにします。
また、変更アイテムの見える化をすることで、例えば、製品変更箇所が穴あけ位置の時は、資料変更箇所として、見積書、製品仕様書、製品部品図を変更しないといけないことが分かるようにし、保管場所や状態の推移を見える化します。
関連の記事⇒生産管理:工場長・製造幹部に求められる3つの能力とは
前の記事⇒生産管理:工場長・製造管理者に必要な維持管理力とは
生産管理・現場改善についての研修・診断・コンサルティングの個別相談・お問い合わせ![]() ![]() |
トヨタ生産方式の改善に役立つツール・帳票
トヨタ生産方式のムダとり、見える化、平準化など様々な管理や改善に役立つ実践ツールや帳票を多数公開中!
ツール使い方や管理・改善手法も動画で解説しています。公開ページはこちら⇒「クリック」
Copyright © 改善と人材育成のコンサルソーシング株式会社