Blog
7.292018
トヨタ生産方式:かんばん方式とは~導入と進め方・事例

ジャストインタイムのトヨタ生産方式を支える「かんばん方式」の導入と進め方
かんばんは、後工程引取りのためのツールです。生産・運搬の指示情報で、何を・いつ・どこに・どれだけ・どういう順序で生産するか、運搬するか指示します。
目で見る管理を実現するもので、改善を促進する道具でもあります。
生産の微調整を行います。大きな需要変動のある工程へは、MRPなどの計画生産スタイルと組み合わせたハイブリッド型の「かんばん」で対応します。
<目次>
かんばんの役割
かんばんの種類
かんばんと平準化
かんばんの流れ
かんばん運用と原単位
かんばんの前提条件と運用ルール
かんばん枠の管理
かんばん総量(運用枚数)管理
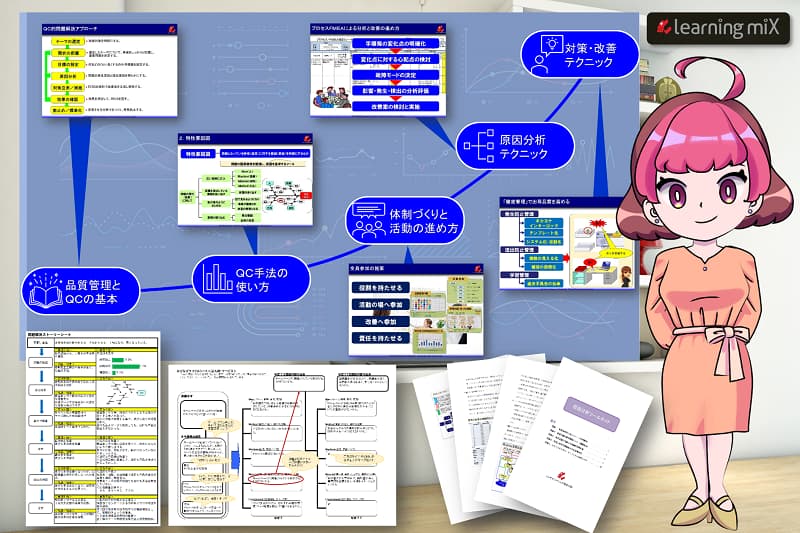
かんばん方式の基本と管理方法
かんばんの役割
「かんばん」は後工程引取りのためのツールです。
あくまでもツールでしかありませんので、「かんばん」を導入したからといって在庫がいきなり削減され、原価が低減されるわけではありません。
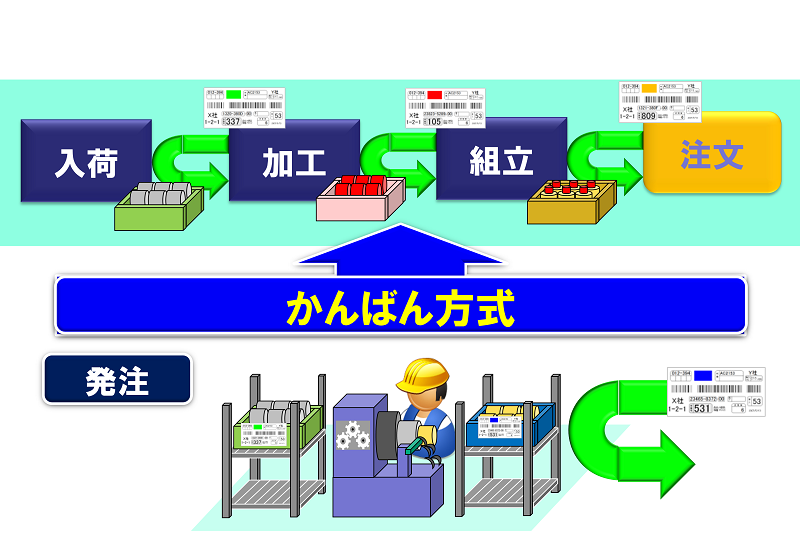
本文
かんばんは、生産・運搬の指示情報
「かんばん」はつくっても良い/引取りして欲しいという情報であり、何を・いつ・どこに・どれだけ・どういう順序で生産するか、運搬するかの指示です。
生産指示の情報は「仕掛けかんばん」によって行われ、引き取り(運搬)指示の情報は「引取りかんばん」によって行われます。
かんばんは、目で見る管理
「かんばん」は、常に現物と一緒に動きます。
つまり、「かんばん」の動きを見ることで、遅れ進みが見えてきます。
「かんばん」が溜まってくれば、作業遅れが発生し、ライン停止がどこかで生じているかもしれません。
逆に「かんばん」が溜まってなければその製品が売れている(回転している)ことの現れです。
作業者はこの「かんばん」情報にもとづき引き取られた分だけ生産します。
「かんばん」が無ければ勝手につくってはいけません。
「かんばん」が無ければ、作業者をあえて手待ちにさせ、異常を検知させます。
このように「かんばん」は、自工程の能力・在庫状況・人員配置・生産の遅れ進みの把握や後工程の作業進捗・緊急度の把握等を「見える化」するための道具となります。
かんばんは、改善の道具
「かんばん」は、改善を促進する道具でもあります。
「かんばん」を使えばモノの動きが見えてきます。
モノの動きに合わせて「かんばん」を抜き挿ししながら、常に在庫をぎりぎりの水準まで下げ、問題が浮かび上がるようにします。
在庫が少なければ現場には常に緊張感が生まれます。
欠品をおこさないための改善がどんどんはかられていきます。
「かんばん」のシェイプアップは、以下のように行います。
①仕掛けかんばん;収容数を減らし、1枚の「かんばん」を何枚かの「子かんばん」に分けます。
②引き取りかんばん;かんばん(納入)サイクルの便を増やしたり、遅れ係数を減らしたりします。
かんばんは、微調整の道具
「かんばん」は生産の微調整を行います。
例えば、赤が300個、青が200個、白が500個という内示で、実際は赤330個、青220個、白450個だったとしてもある一定範囲内であれば「かんばん」で対応できます。
したがって、「かんばん」は大きな需要変動のある工程に、単独で導入することはできません。
無理やり「かんばん」を導入しても振れの大きな製品では不可能であり、それが現品票のような使われ方しかできなくなってしまいます。
このように大きな需要変動のある工程へは、MRPなどの計画生産スタイルと組み合わせたハイブリッド型の「かんばん」で対応しなければなりません。
かんばんの種類
かんばんには、「生産指示かんばん」・「引き取りかんばん」・「特殊かんばん」等があります。
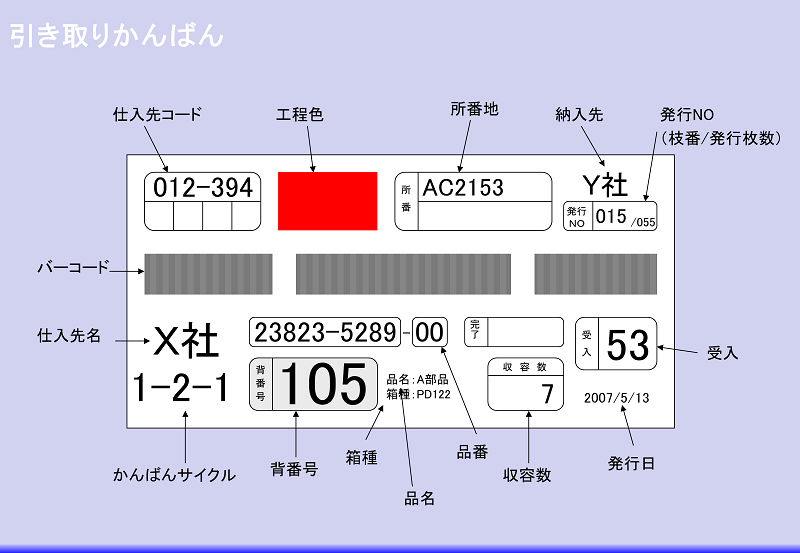
本文
生産指示(仕掛け)かんばん
工程内の生産を指示するためのかんばんで、「工程内かんばん」と「信号かんばん」があります。
「工程内かんばん」は、工程内の仕掛けに用い、工程に引き取られた量を引き取られた順序で後補充生産するために使うかんばんです。
「信号かんばん」は、ロット生産工程の仕掛けに用い、一定量になった段階でかんばんが外れロット生産指示となり、在庫が無くなるタイミングと生産が完了するリードタイムを見比べながら仕掛けを行います。形が三角形をしているので「三角かんばん」とも呼ばれます。
引き取りかんばん
「引き取りかんばん」は運搬を指示するためのかんばんで、「外注部品引き取りかんばん」と「工程間引き取りかんばん」があります。
「外注部品引き取りかんばん」は、外注先を前工程とし、かんばんが外れた分だけ外注先が納入するために使うかんばんです。
「工程間引き取りかんばん」は、社内で後工程が前工程から必要なものを必要な時に必要な量だけ引き取るために使うかんばんです。
特殊かんばん
「特殊かんばん」には、「臨時かんばん」・「先行かんばん」・「プールかんばん」などがあります。工程間に直差等がある場合やあらかじめ計画的につくりだめする場合など特殊な場合に用いられ、かんばんが何度も回転することは無く発行後回収されます。
かんばんと平準化
かんばんと平準化
かんばん運用は、平準化が必要不可欠となります。
平準化とは
全ての工程で量の平均化がされるためには、最終組立てラインの「量」を平均化しただけでは不十分であり、「種類」についても平均化しなければなりません。
つまり、製品をAAABBBCCCとつくるのではなく、ABCABCABCとういように「種類」も平均化します。
これにより在庫を持たずに生産能力にも余裕を持って対応することが可能となります。
平準化がされていなければ、設備・人・在庫等をピークに合わせて準備してしまい原価の高いものになってしまいます。
負荷の平準化
需要は日々変動し、受注量にはバラツキが生じます。
そのバラツキをそのままの形で生産すれば、生産能力や人員に過不足が生じ、あるときは設備余剰や手待ち、あるときは設備能力不足や人手不足になります。
そこで、日々の需要のバラツキを月単位あるいは週単位でならし、平準化します。これが負荷の平準化です。
能力の平準化
いくつかの工程にまたがって製品が出来上がる場合、その各工程の能力は必ずしも同じになりません。
例えば、A工程の能力が100個/日、B工程の能力が140個/日、C工程の能力が80個/日、D工程の能力が60個/日と仮定した場合、
同一日にその製品をつくろうとすれば、
一番能力の劣るD工程が制約条件となり60個/日しかつくることはできません。
B工程の能力が2倍以上あってもその能力でつくればそれは在庫となってしまい、C工程の前で停滞してしまいます。
このような時は、
ボトルネックとなる工程の能力を上げ、4つの工程能力の均一化を図っていきます。
水がパイプを通って流れる場合、その直径の大きさの流量しか流れないように、径の大きさがバラバラであれば一番小さな径の大きさでしか流れません。
大きな径のパイプを入れた工程は、設備余剰と化してしまいます。これが能力の平準化です。
かんばんの流れ
かんばんの流れ
「生産指示(仕掛け)かんばん」・「引き取りかんばん」は、工程内やサプライヤー間を循環します。
かんばんのまわし方
「引き取りかんばん」は以下のように流れていきます。
①製品が出荷され、「仕掛けかんばん」が外れます。
②外れた「かんばん」は、かんばんポストに入れられます。
③かんばんポストの「かんばん」は、かんばん置き場に移動されます。
④かんばん置き場の「かんばん」は、トラックに載せられます。
⑤「かんばん」はサプライヤーに届けられます。
⑥トラックは、「引取りかんばん」の量だけサプライヤーから製品を積み込みます。
⑦トラックは、製品を指定されたストアに納めます。
「生産指示(仕掛け)かんばん」は以下のように流れていきます。
①引き取りかんばんにて出荷指示がきます。
②引き取り情報にもとづき、ストアから製品を出荷します。
③ストアから引き取られた分だけ、「仕掛けかんばん」を「引き取りかんばん」に換えて外します。
④「仕掛けかんばん」が外れた量だけ後工程が前工程のストアから製品を引き取ります。
⑤ストアから引き取られた分だけ、「仕掛けかんばん」を外します。
⑥同様に後工程が前工程のストアから製品を引き取ります。
⑦外れた「仕掛けかんばん」をかんばんポストに入れます。
平準化仕掛けポスト
かんばん置き場には、平準化仕掛けポストを設置します。
縦軸に製品名、横軸に時間を入れ、仕掛ける順番と遅れ進みのチェックができるように指定席や自由席を設けて、平準化をはかります。
かんばん運用と原単位
「かんばん」を運用していくには、各工程間の流れをつくり、流れる単位(原単位)を合わせる必要があります。
流れを整理する
製品毎にどのような工程を通り出荷されるのかという工程順を整理します。
運搬・仕掛けの原単位を合わす
各工程で仕掛り単位が異なる場合、「かんばん」を入れても工程ごとに端数が生じるため管理がしにくくなります。
そこで、収容数をあわせ、仕掛り単位はなるべく収容数の整数倍になるようにします。
かんばんの前提条件と運用ルール
「かんばん」は万能ではありません。製品や生産方法により適用できない場合もあります。
かんばんの前提条件
「かんばん」の運用には以下の条件が必要となります。
①繰り返し生産品であること;
毎日生産することなくたまにしか生産しない品目や1品生産の品目等には使えません。
②平準化されていること;
平準化とは、売りにつながったモノの種類と生産量の平均化です。
ある時間軸で区切り、例えば9時・10時・11時・・・でその種類と量が大きく異なることがあってはなりません。
③工程が安定していること;
製品の不良率は低くなければなりません。
④「かんばん」は微調整として使うこと;
需要変動の大きな製品や生産方法には対応できません。
対応する場合は、ハイブリッド型のかんばんとなります。
⑤店を設ける;
店とよばれるストアを各工程の後に設けます
⑥荷姿、容器を設定し、収容数は小さくする
1個流しを目指しつくり/運搬の単位を小さくします。
かんばんの運用ルール
①不良品を後工程へ送らない、製品は100%良品であること;
「かんばん」の指定数量が完成しても、そのうち何割かが不良品であっては「かんばん」は回りません。
②「かんばん」が外れた分だけ後工程は前工程に取りに行く;
前工程が後工程に押し込みをしてはいけません。
③前工程は「かんばん」が外れた量だけ外れた順番に生産する;
生産の優先度を考慮します。
④「かんばん」の無い時は、造らない、運ばない;
「かんばん」が無い時に見込みでつくってはいけません。
⑤かんばんは現物に必ず付ける;
情物一致で、モノと情報が一緒に動きます。
⑥かんばんは容器ごとに1枚つける;
1容器1情報にします。
⑦かんばんは最初の1個を使用するときに外してポストにいれる;
容器内のひとつに手をつければ「かんばん」が外れるようにします。
⑧欠品の時は、できあがり次第後工程に届ける;
異常なかんばんの振れが出た時は、ルールを決めて対応する。
⑨使用部署が管理する;
かんばん枠の管理
かんばん枠の管理
売れるスピードに合わせて、「枠」の拡大・縮小をはかります。
かんばん枠とは
「かんばん」は±10%程度以内の振れならば、かんばん内容や枚数を変えずに対応できますが、大きな振れには対応できません。季節変動などで需要の大きな月と小さな月が存在する場合、内示情報で生産量が仮に20%増加すると見込まれると、生産「枠」を20%拡大します。
生産枠の拡大は、
①残業
②受援
③休日出勤
④2勤3勤体制
⑤外注化
⑥ライン増設
⑦ラインの専用化
⑧タクトタイム短縮(能力増強)
⑨外段取り化
などを行い、量の増大に対応します。
反対に、生産量の減少が見込まれる場合は、生産枠の縮小を
①教育・訓練
②応援
③有給キャンペーン
④ライン統合・混流化・編成替
⑤タクトタイム伸長(1人作業化等)
⑥内段取り化
などを行い、量の減少に対応します。
枠の拡大・縮小は計画的に
枠の拡大・縮小は常に余裕をもって仕事をしている場合は別ですが、通常能力ぎりぎりの状態で生産している場合、簡単には変動することができません。
設備の増強をした途端、受注が減ってしまっても困るし、人手不足の中で急に受注が増えても人材はすぐには確保できないし、育成もできません。
かんばん総量(運用枚数)管理
「かんばん」は追加・間引きをリアルタイムで行い、メンテナンスを小まめに繰り返します。
かんばんの運用総枚数は最小限にしなければならない
「かんばん」の総枚数は在庫数を表します。
「かんばん」が停滞していれば、製品回転率が落ちていて在庫となっており、逆に「かんばん」が流動していれば、製品回転率が上がっていて欠品の可能性が出てきます。
かんばん総量は、日々見直しをし、追加・間引きをリアルタイムで行っていきます。つまり、売れるスピードとつくるスピードの同期をはかります。
かんばん枚数の決め方(理論値)
日当たり必要量/かんばん収容数 ×(正味リードタイム+1+α)=かんばん総量 *α=安全値
※理論値ではこのようになりますが、実際は現地現物でかんばんの動きを見ながら抜き挿しします。
サプライチェーン改善を進めるためにかんばん方式改善リーダーをつくる
トヨタのかんばん方式は、かんばんによる後工程引き取りによって、各工程を連結し、連動させるサプライチェーンを実現します。
連携したサプライチェーンによって、必要のモノを必要なときに必要なだけつくるJustInTimeを実現します。
JustInTimeによって、在庫を極限まで減らし、欠品をなくし、不要不急のものづくりのムダをなくして原価を低減します。また、JustInTimeがラインの改善を促し、QCDレベルの高い筋肉質なラインへと成長させます。
かんばん方式のサプライチェーン改善は、かんばんと後工程引き取りによって、工程の連結・連動をめざす改善スタイルです。
このような改善を実現するためには、かんばんとストアによるPULL型生産管理システムの構築のできるサプライチェーン改善リーダーの育成が不可欠です。
かんばん方式による工程連結・連動によってライン改善を促進させ、QCDレベルの高い筋肉質なラインづくりをめざしましょう。
次の記事⇒工程管理の極意は流れの中のQCDを管理すること
前の記事⇒整流化改善とは~進め方・事例
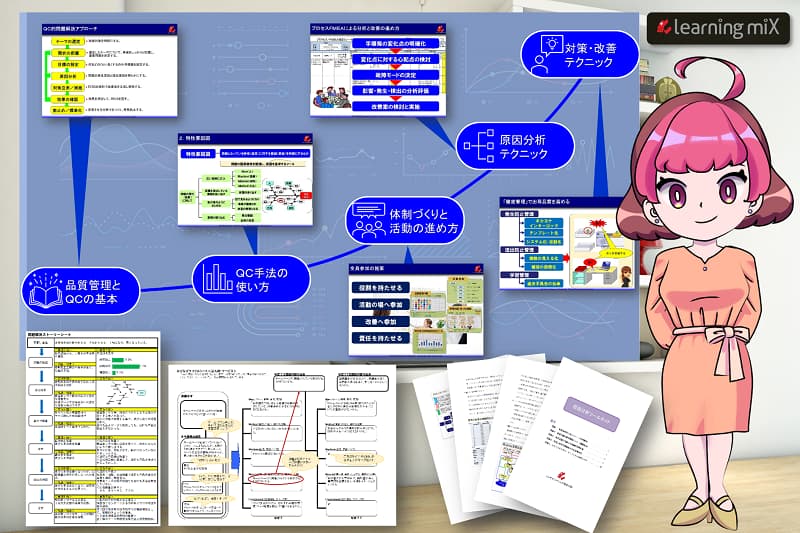
かんばん方式の基本と管理方法
トヨタ生産方式の改善に役立つツール・帳票
Copyright © 改善と人材育成のコンサルソーシング株式会社